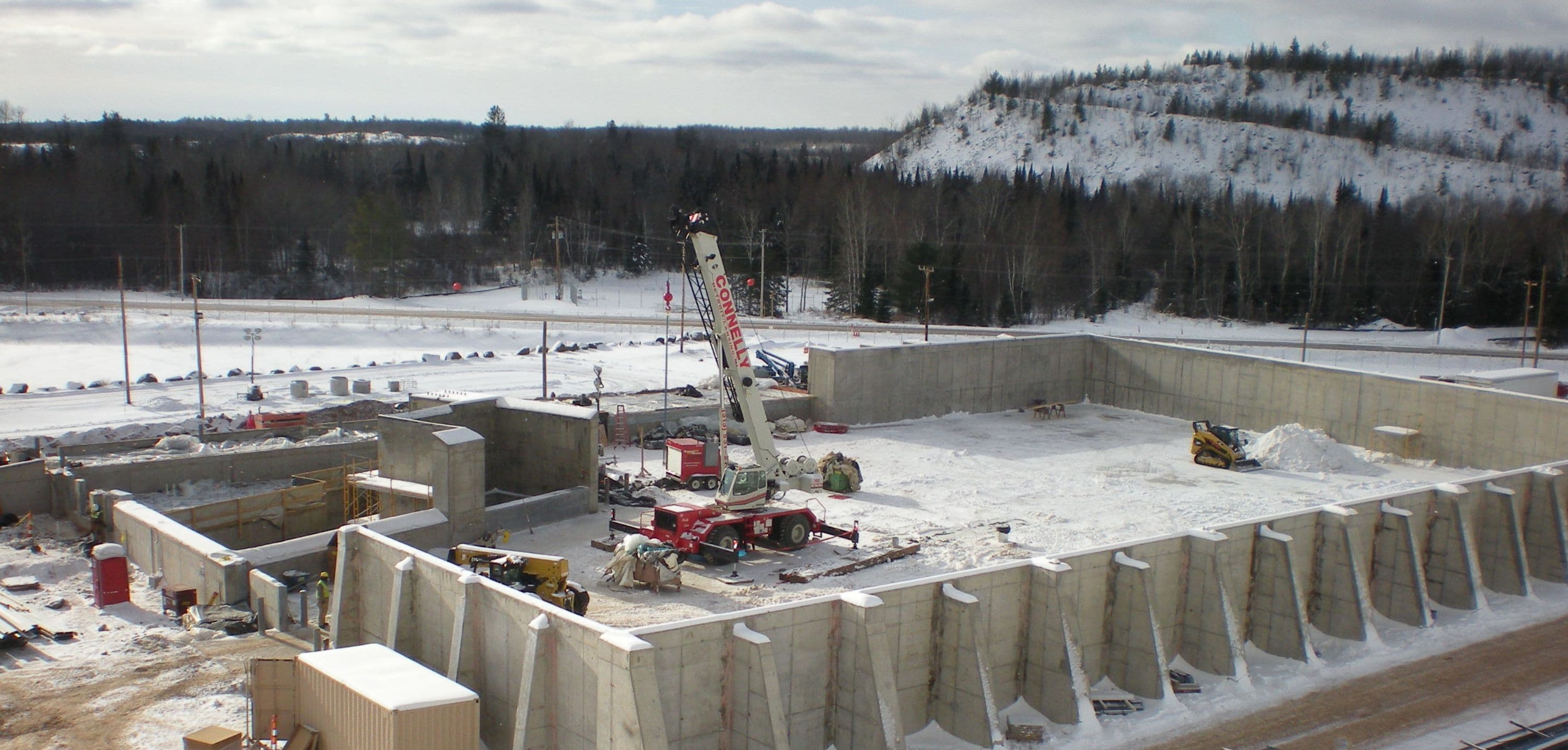
Lundin Mining Eagle Mine
Client: Lundin Mining
Location: Upper Peninsula, MI, U.S.
Business Segment: Urban Solutions
Industry: Mining & Metals

Executive Summary
The Lundin Eagle Mine is an underground, high-grade nickel and copper mine located in the Upper Peninsula in the state of Michigan. Fluor provided engineering, procurement and construction management (EPCm) services for the mine, mill process plant and all associated facilities. The facilities at the mine site include aggregate storage, course ore storage, portal fans and heaters and truck shop. The mill site areas include crushing, conveying, dust collection, grinding, classification, floatation and regrind, concentrate thickening and dewatering as well as tailings disposal.
The mill property was a former iron ore processing facility built in the 1950s and included the revamp of several structures and the construction of new facilities. The mill produces a nickel and copper concentrate to be transported via rail car directly to smelter facilities within North America or to ports for shipment overseas.
Client's Challenge
In building Michigan's first new mine in decades, Lundin was dedicated to safety, protecting the environment and putting area people to work. Eagle Mine obtained the permits necessary to refurbish and operate the mill in 2010. Between 2009 and 2011, Eagle invested more than $5 million in clean-up and environmental reclamation activities of historical mining waste.
Construction and equipment upgrades to the Mill began in 2012. The facilities were initially developed to process 2,000 metric tons per day of ore and 800 metric tons per day of nickel and copper concentrates.
It was expected that approximately 300 million pounds of nickel, 250 million pounds of copper and minor amounts of other minerals would be produced from the mine. These minerals provide the metals that are used in state-of-the-art technologies used by many Michigan-based manufacturers.
Lundin Mining would access the deposit through an underground mine development. The entire project site required less than 120 acres.
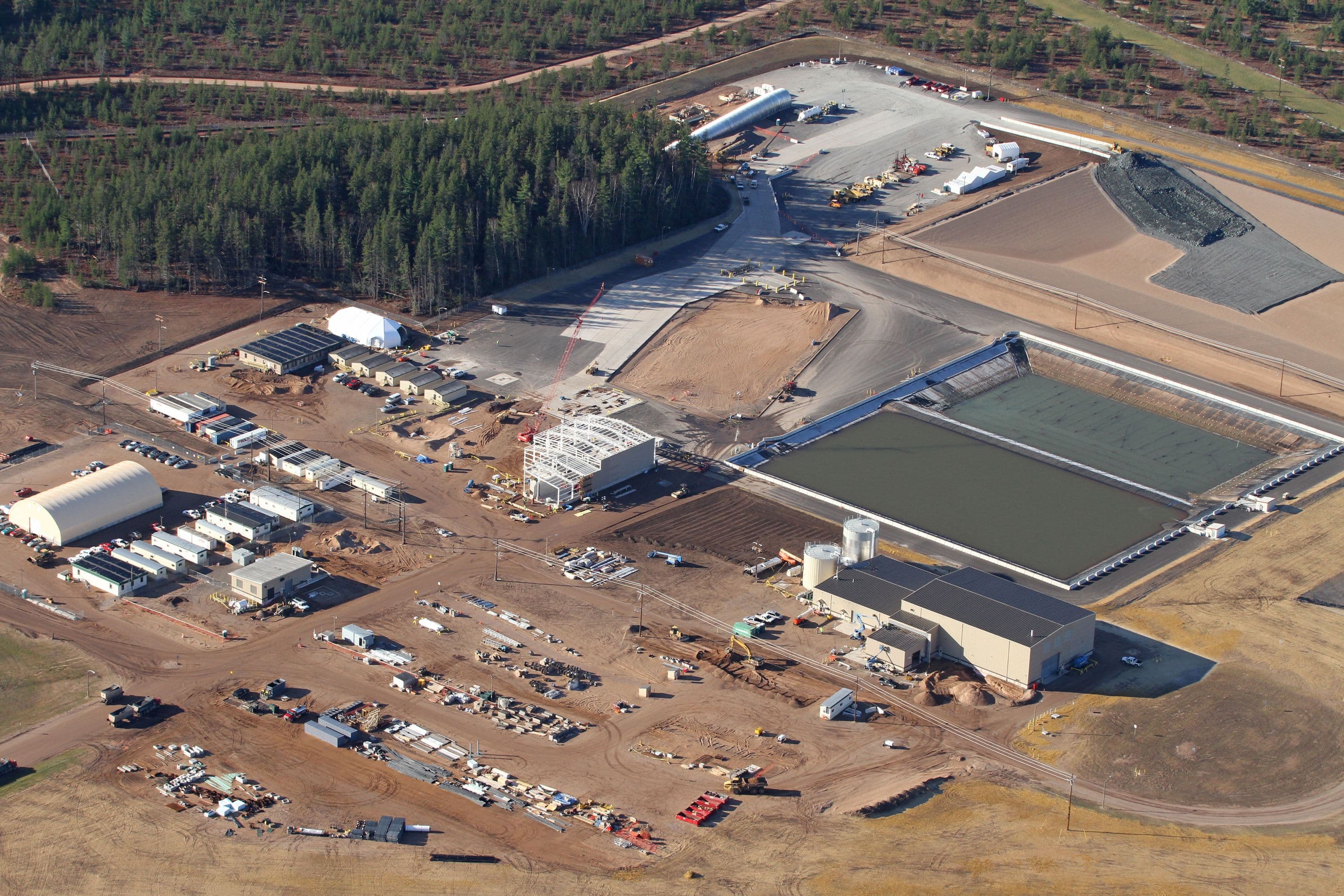
Fluor's Solution
Our scope of facilities involved mine surface facilities, mill rehabilitation, an ore transportation road and power line construction. Through careful design and permitting requirements, noise and odor from mining operations was kept to a minimum, and the relatively small footprint of the project meant less impact to the environment and the community.
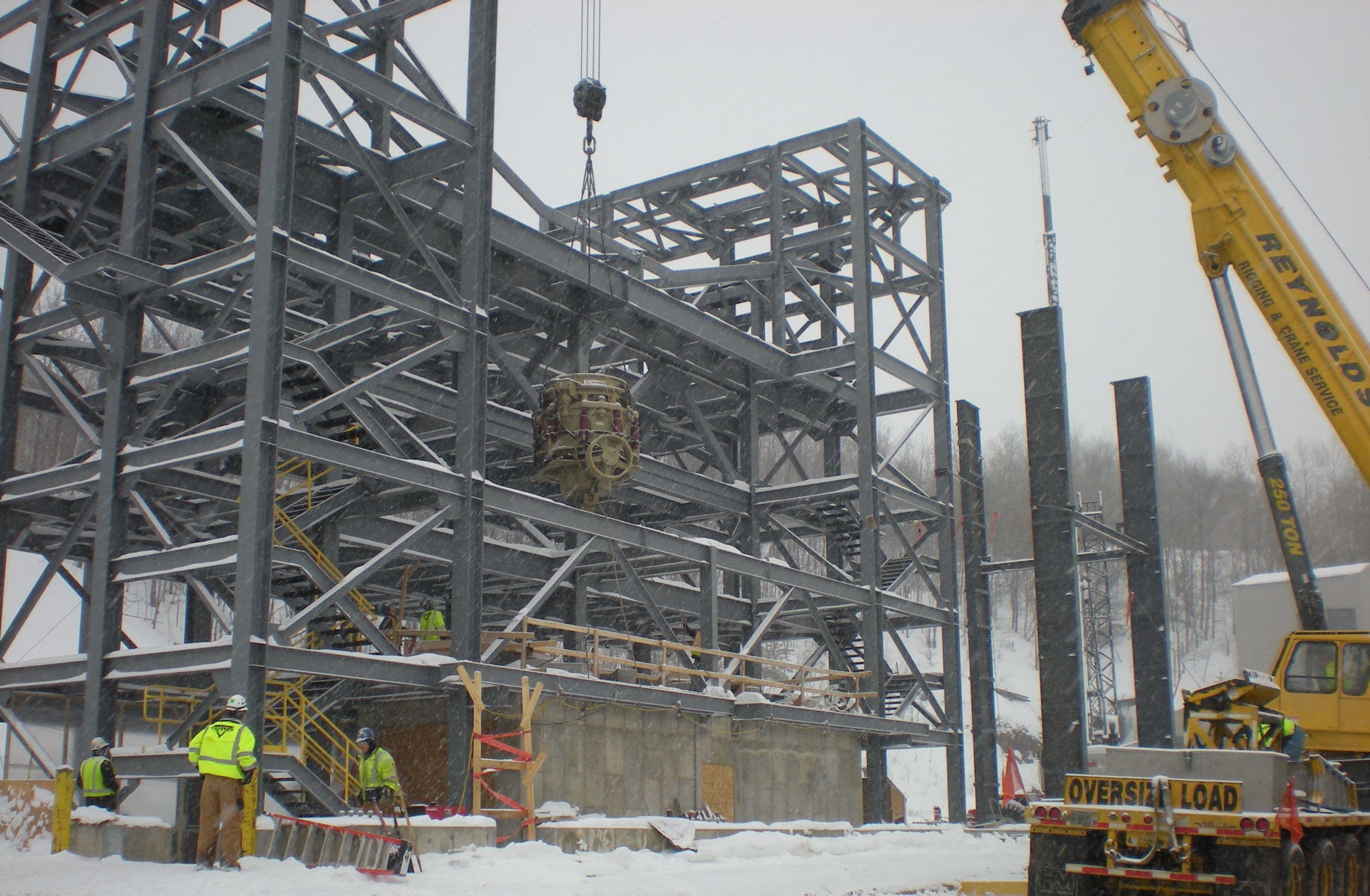
Conclusion
Once the ore was brought to the surface, it would be transported by truck to the Humboldt Mill for processing, then by rail to an offsite facility for further refinement. With respect to environmental sensitivity and sustainability, the large majority of the land owned or leased by Lundin Mining remained undisturbed by project activities and is available for camping and other recreational activities. During construction, peak manpower was approximately 700.
When mining operations are completed, restoration will be implemented quickly and efficiently. In order to preserve the environment, it is Lundin's goal to see that any land that has been disrupted during the mining process will be returned to a natural state.
&w=3840&q=75)