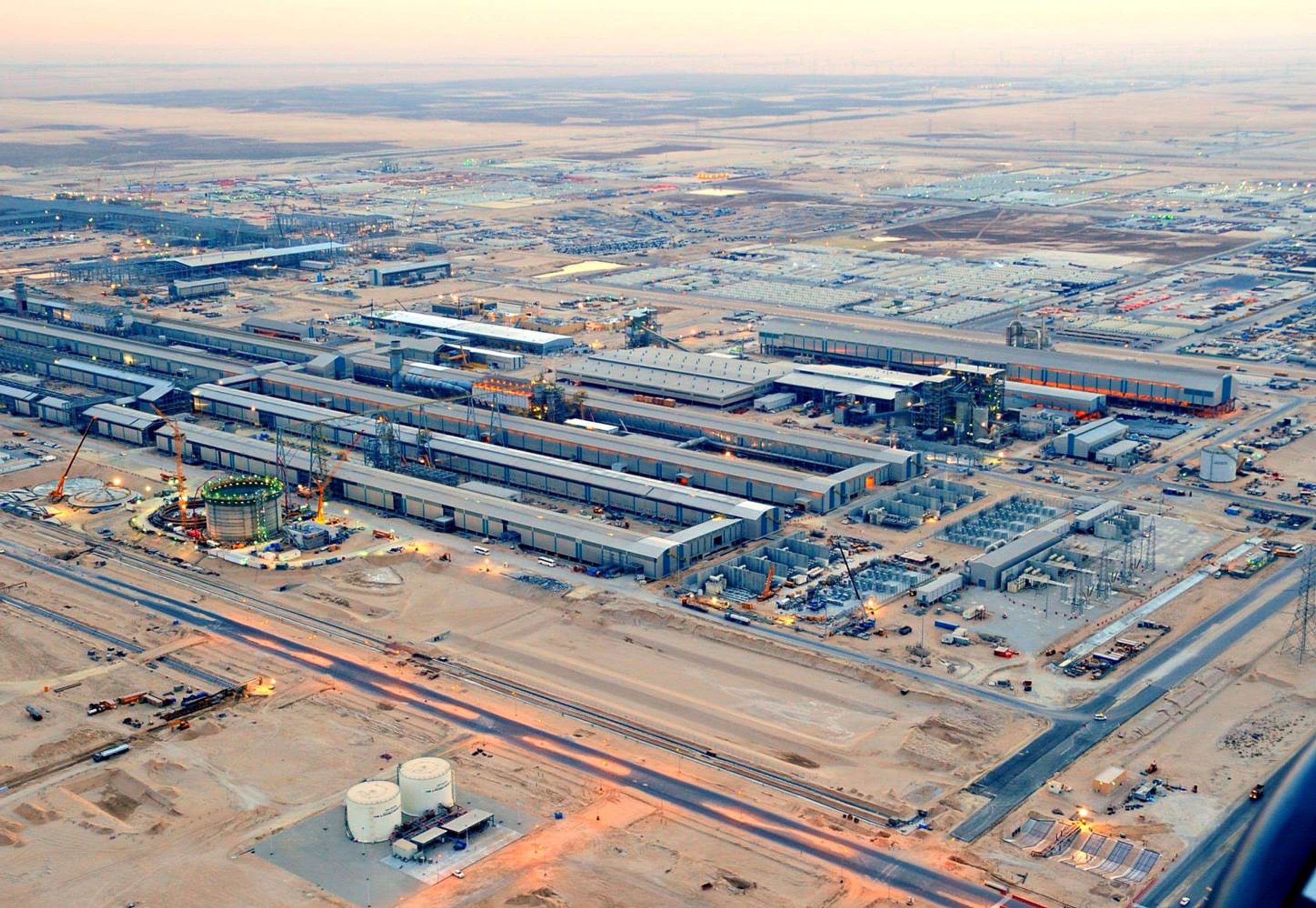
Ma’aden Aluminum
Client: Saudi Arabian Mining Company (Ma’aden) and Alcoa (JV)
Location: Ras Al Khair, Saudi Arabia
Business Segment: Urban Solutions
Industry: Mining & Metals

Executive Summary
The Ma’aden Aluminum Project was a $10.3 billion greenfield project with two major components in Saudi Arabia: a bauxite mine at Al Baitha and the Ma’aden Aluminum complex located at Ras Al Khair (RAK), a purpose-built Mineral Production City 220 kilometers north of Al Khobar. The aluminum complex located at RAK consisted of an alumina refinery, smelter, rolling mill and automotive sheet plants with the associated infrastructure.
Fluor provided project management consultant (PMC) services for the overall program, including the bauxite mine, alumina refinery, aluminum smelter, rolling mill, automotive sheet plant and all associated infrastructure.
We were also responsible for the following scopes of work:
Integrated infrastructure engineering, procurement and construction management (EPCm) services
Bauxite mine & alumina refinery
Rolling Mill
Automotive sheet EPCm services
The site infrastructure included an Alcoa-designed, first-of-its-kind engineered wetlands wastewater management system that naturally treats sanitary and industrial wastewater without chemicals or odors for reuse in the manufacturing process and for irrigation. Based on the cost savings realized on the rolling mill project, Ma’aden awarded the engineering, procurement and construction management contract for the aluminum sheet facility to Fluor in 2012. The sheet facility was a late addition to the overall project and was important to the development of Saudi Arabia’s automotive manufacturing capability.
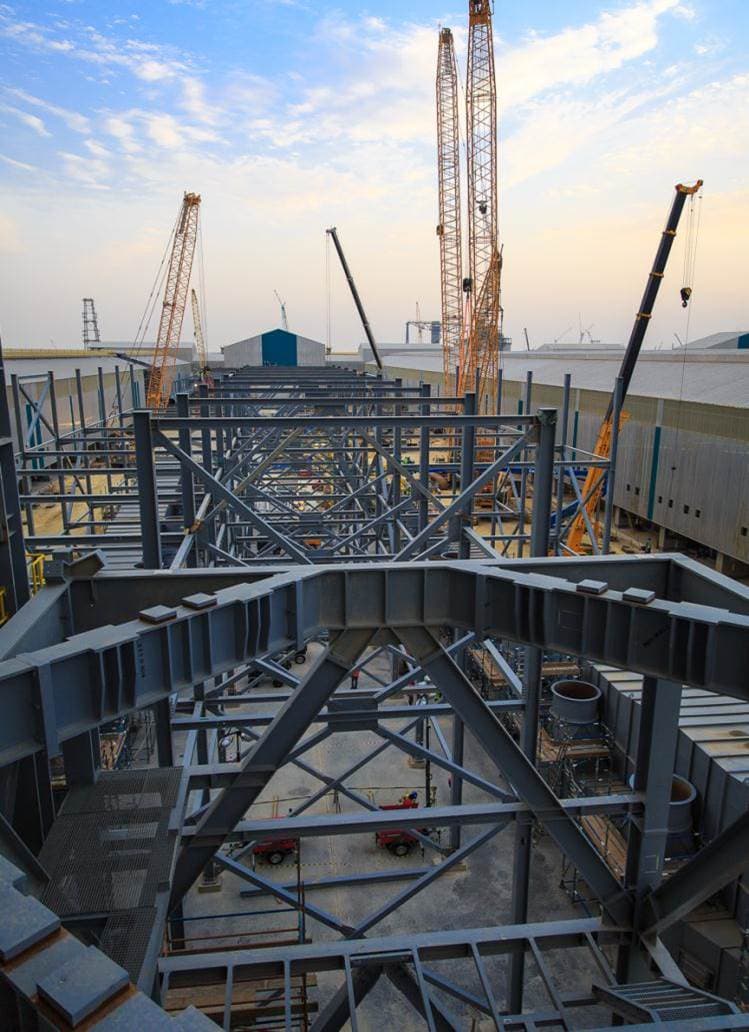
Client's Challenge
The Saudi Arabian Mining Company (Ma’aden) and Alcoa formed a 75/25 joint venture to oversee design, procurement, construction, commissioning, operations and maintenance of the Ma’aden Aluminum Complex and Mine.
For Ma’aden, the project represented the most significant investment to date in the Kingdom's development goal of adding minerals and metals as the third pillar of the country’s economy, behind oil and natural gas. Ma’aden also saw this project as making strides toward achieving the Kingdom’s other three strategic goals: capacity building, quality job creation and balanced regional development. For Alcoa, the project would be the lowest-cost aluminum production complex within the Alcoa system, in line with its strategy to lower its overall production cost base and expand its market in the Middle East region.
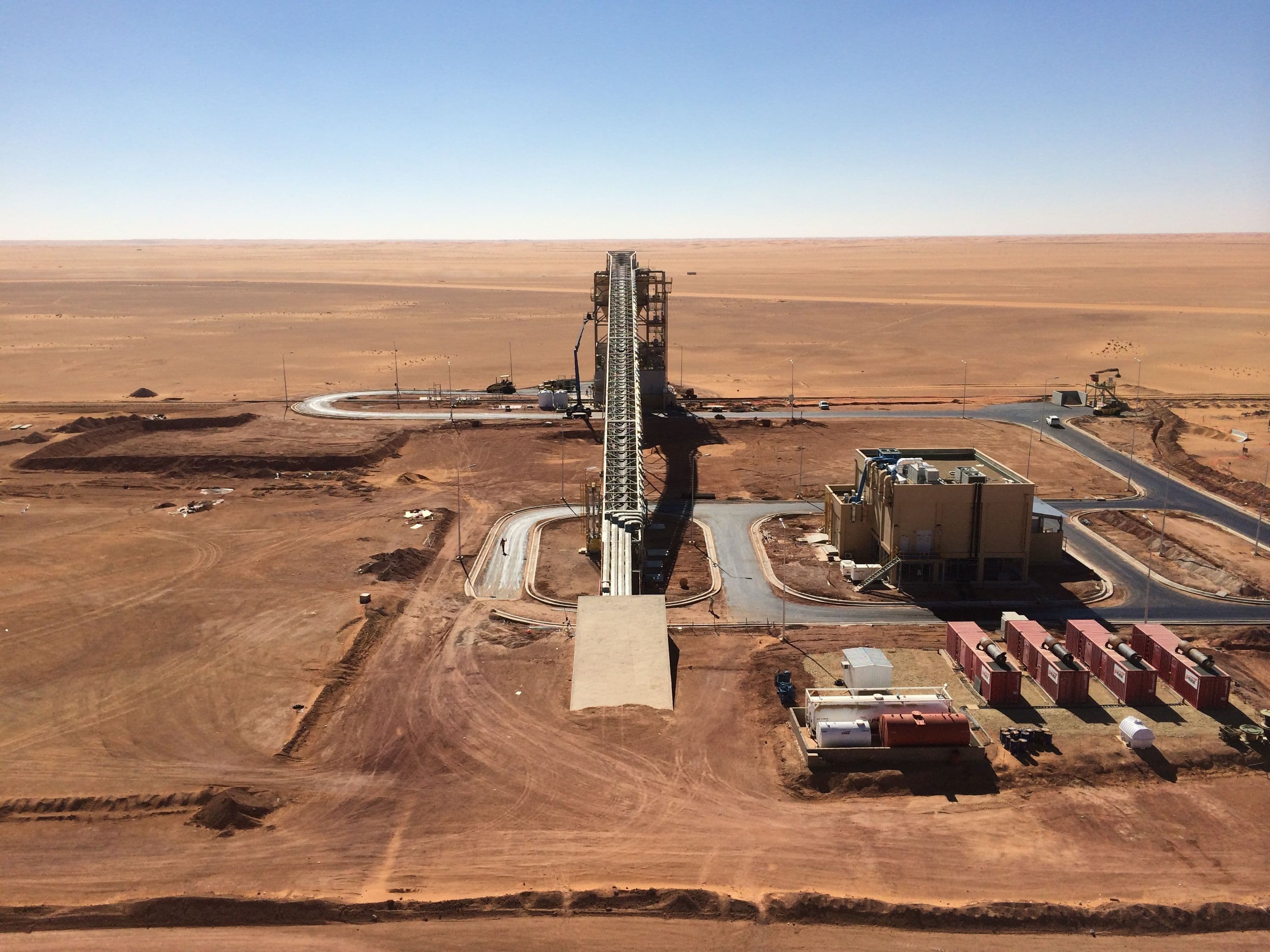
Fluor's Solution
Fluor was awarded PMC services for the large-scale Ma’aden Aluminum Complex. We also provided PMC and EPCM services on individual projects. The savings within the overall program allowed Ma’aden to add the automotive sheet facility later in the project, executed as an EPCm contract by Fluor. A summary of the various project scopes follows:
Integrated Infrastructure Project - Our scope comprised integrated infrastructure EPCm, including a 27-kilometer gas pipeline, utilities, security and buildings. The Ma’aden Aluminum Site Complex covers 20 square kilometers.
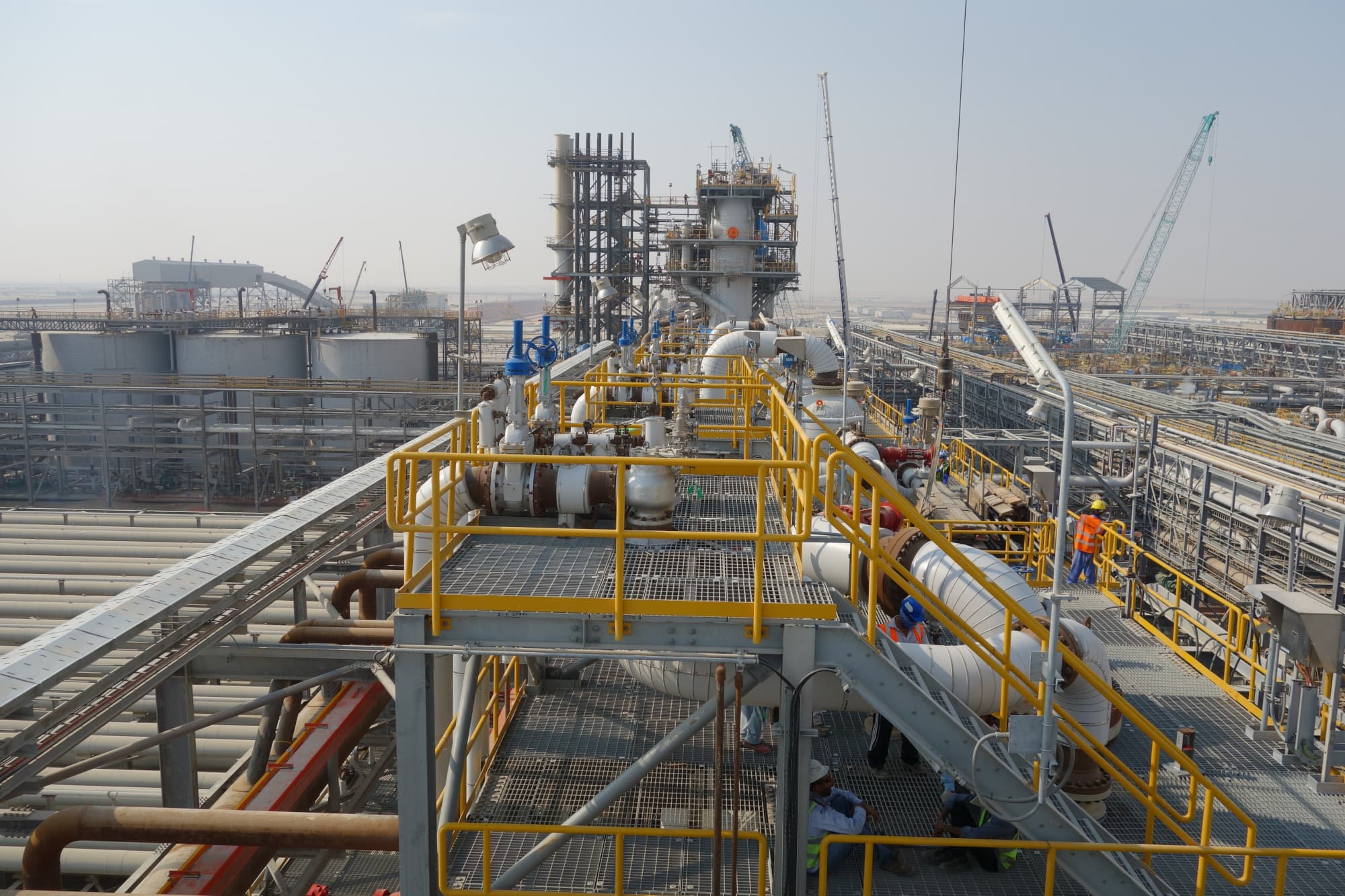
Bauxite Mine & Refinery Project – WPF JV originally awarded EPCm services, which were converted to PMC services after the project was awarded on lump sum bases to several contractors, on the mine and refinery. The mine has a capacity of 4 million metric tons per year. The refinery’s capacity is 1.8 million metric tons per year. Bauxite is shipped from the mine to the refinery by rail, approximately 560 kilometers west of the integrated site and port facilities. At the refinery, the bauxite is crushed, refined and converted to alumina, which is then conveyed to the smelting facility.
Construction of the refinery included installation of:
225,000 m3 of concrete
42,000 tons of steel
20,000 tons of tanks
450,000 meters of piping
40,000 tons to equipment
4.1 million meters of cable
Smelter – We provided PMC services for the aluminum smelter where commercial aluminum ingots and slabs are produced and transported for processing through the rolling mill and/or automotive sheet facilities.
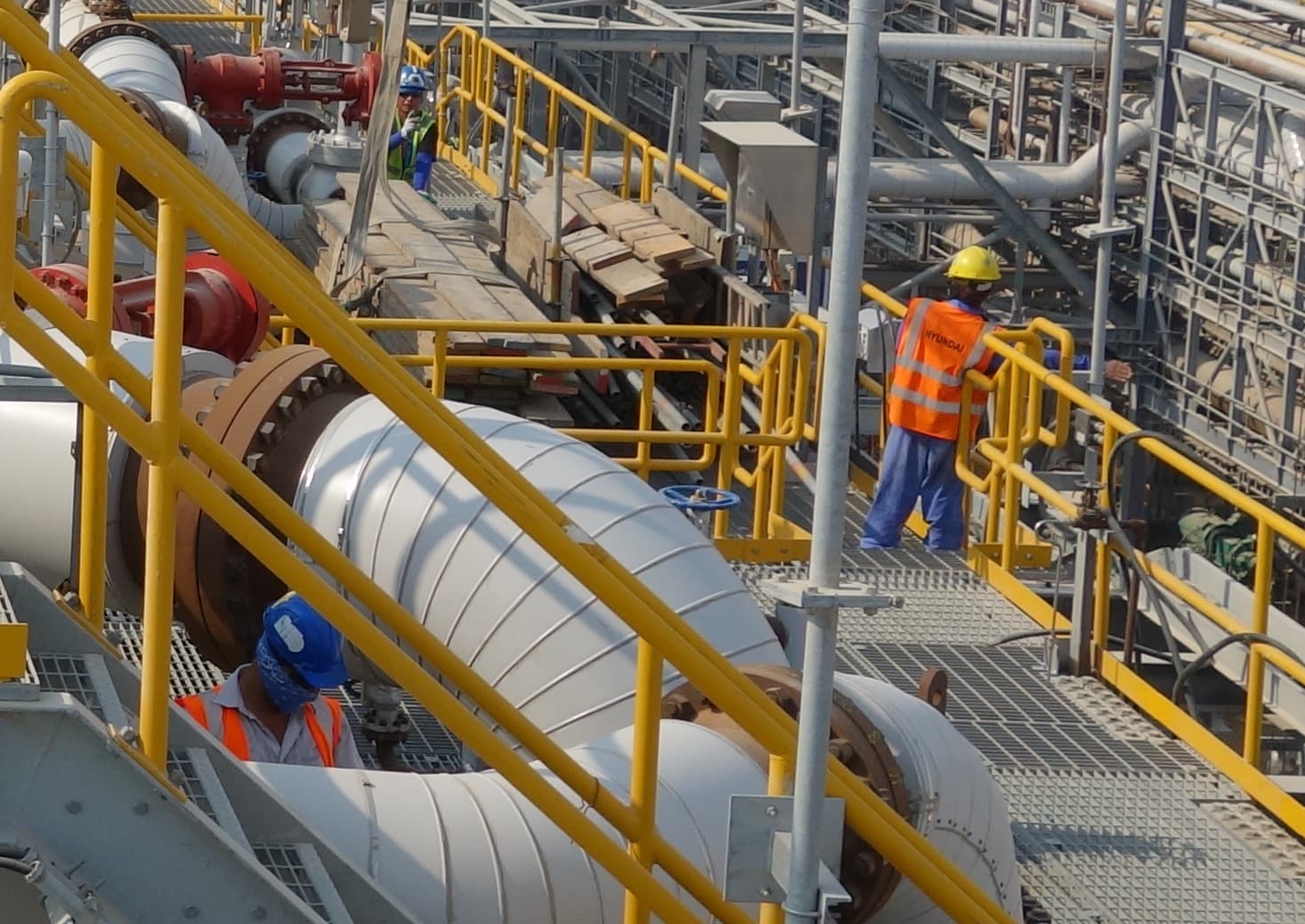
Aluminum Rolling Mill Project – We completed Phases 2 and 3 of the front-end loading (FEL) portion of the rolling mill project. EPCm was then awarded as a lump-sum contract to another firm with Fluor providing limited oversight. We later added construction coordination and turnover resources to support startup and turnover to Ma’aden. Fluor and the contractor achieved over 40 million safe work hours.
Automotive Sheet Project – As a result of cost savings from other sub-projects, Ma’aden awarded Fluor FEL and EPCm for the 50 kta capacity automotive sheet facility. The project was a late addition to the overall scope and was important to the development of automotive manufacturing capacity in the Kingdom. We successfully completed the EPCm contract on the automotive sheet facility in 2015.
Operations & Maintenance (O&M) – Our O&M team worked with the owner’s team during FEED and mobilized to the site providing operational readiness technical services and pre-start-up deliverables. This portion of the project ended in December 2014.
The Integrated Aluminum Complex project and sub-projects were staffed during a peak time in the mining and metals business, so our mining & metals group was supplemented with Fluor's extensive global resources from across other business lines.
Total peak workforce on site was 36,000, covering 30 different nationalities, with a Saudization content of 23%.
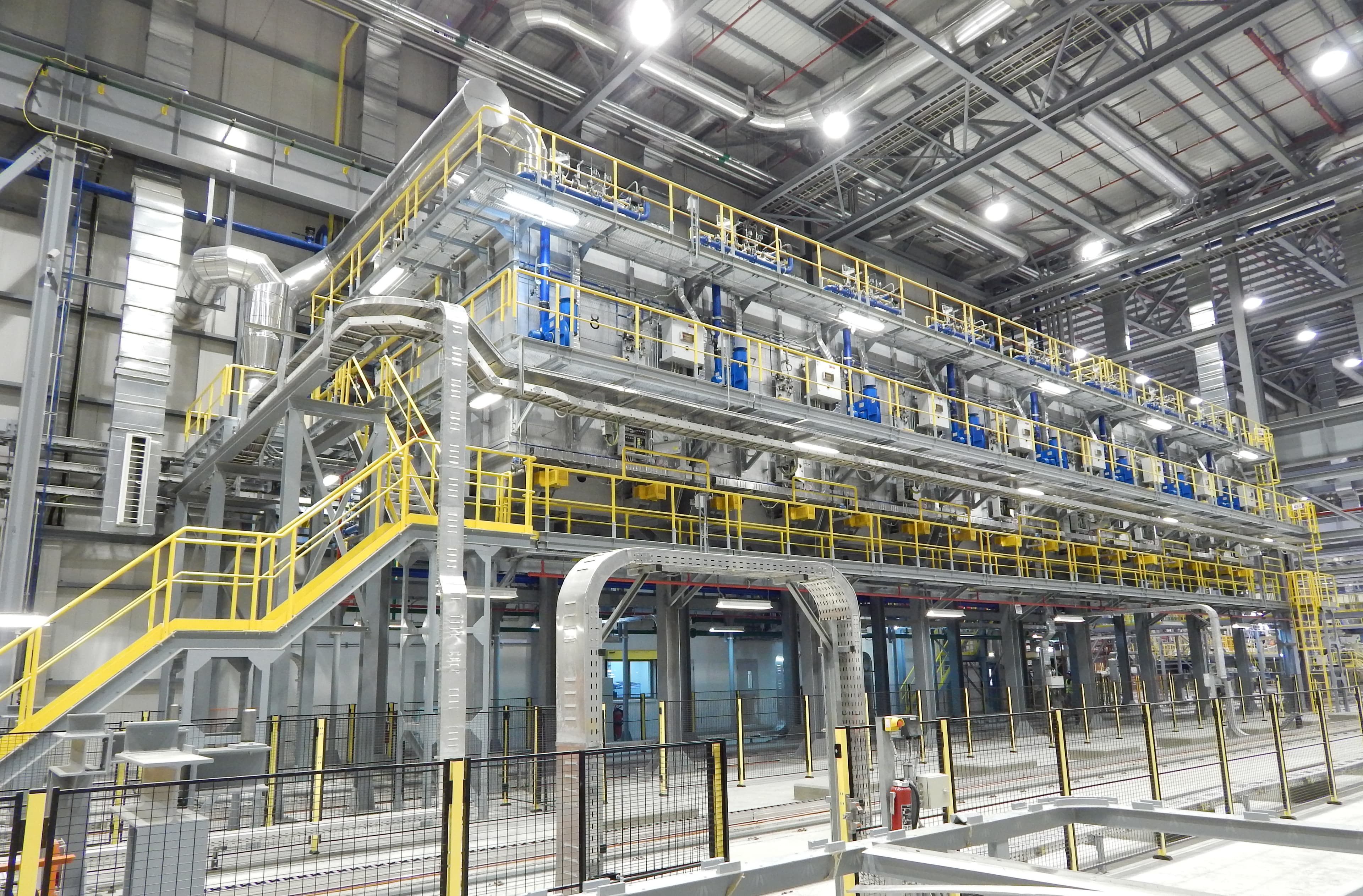
Conclusion
Fluor’s participation in all of the projects within the Aluminum Complex delivered an integrated solution to Ma’aden. We provided the resources and showed the flexibility to change execution strategies to meet Ma’aden's objectives. The savings realized from the revised execution strategies allowed Ma’aden to invest in the automotive sheet facility.
Our successful delivery of the integrated Ma’aden Aluminum Complex positively influenced Ma’aden’s decision to contract with us for the EPCm of the company’s new phosphate plant in Umm Wu’al in northern Saudi Arabia.
The program worked a total of 29.5 million hours and achieved a total case incidence rate (TCIR) of 0.08 and a DART-R rate of 0.01.
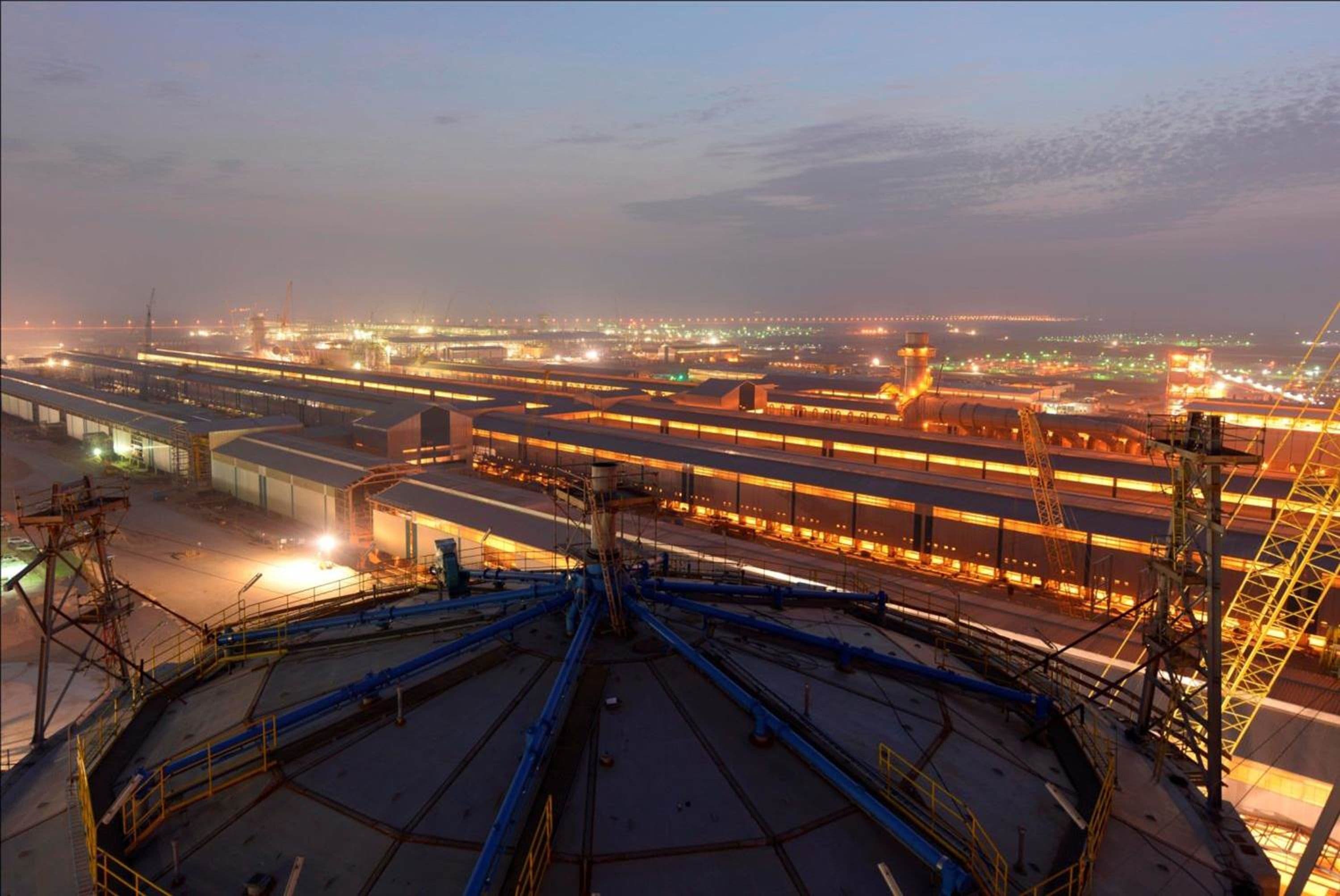
Project Gallery
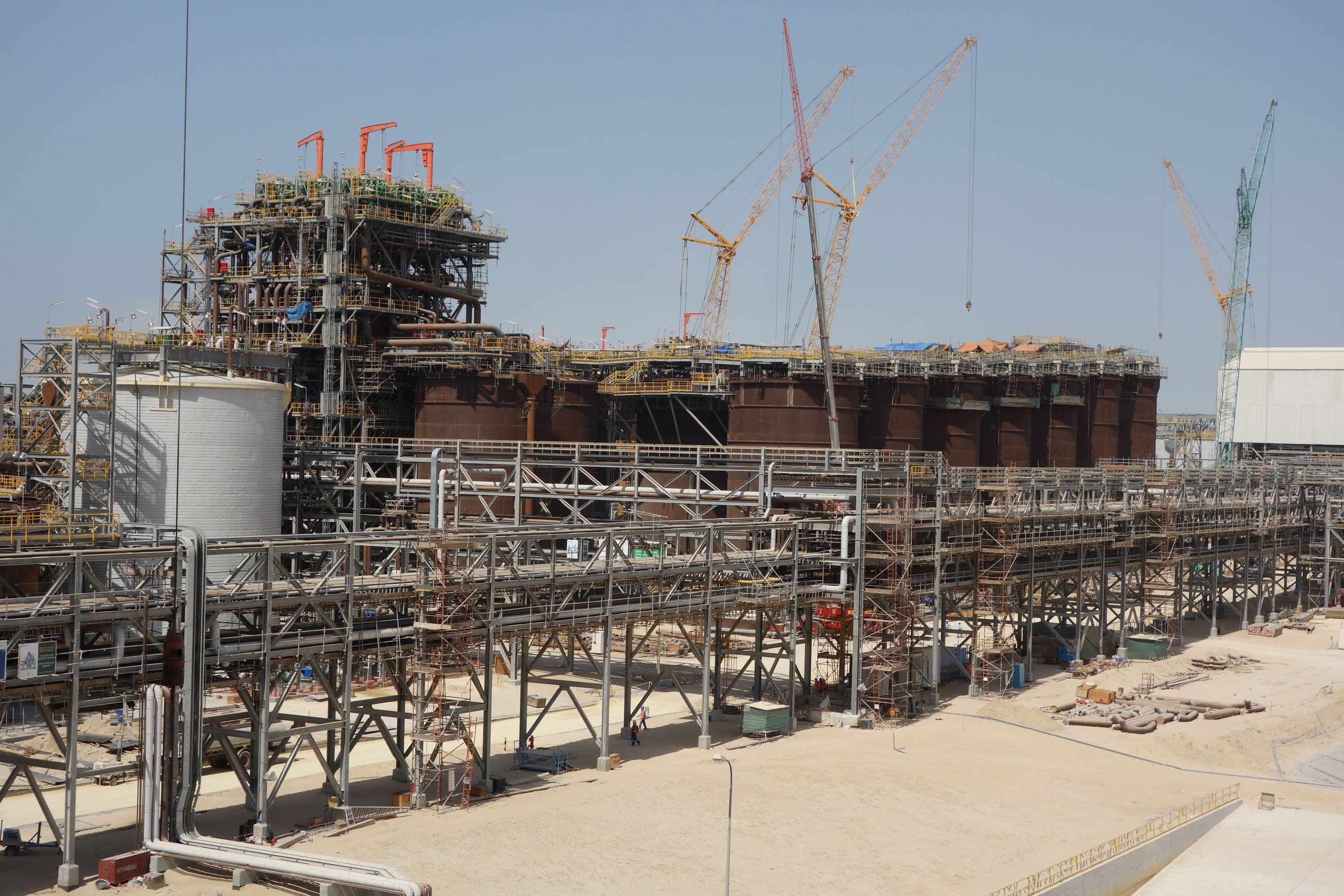
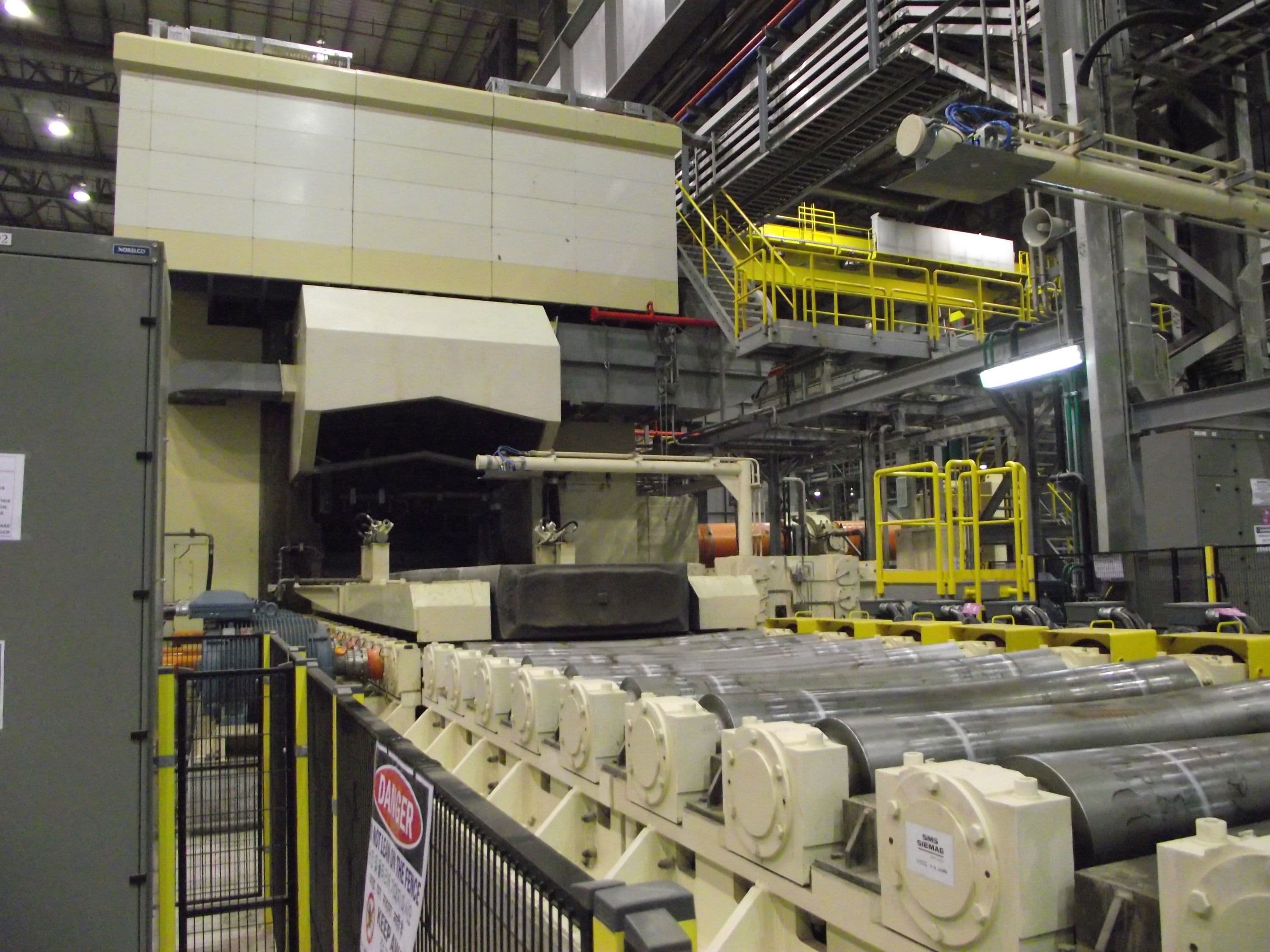
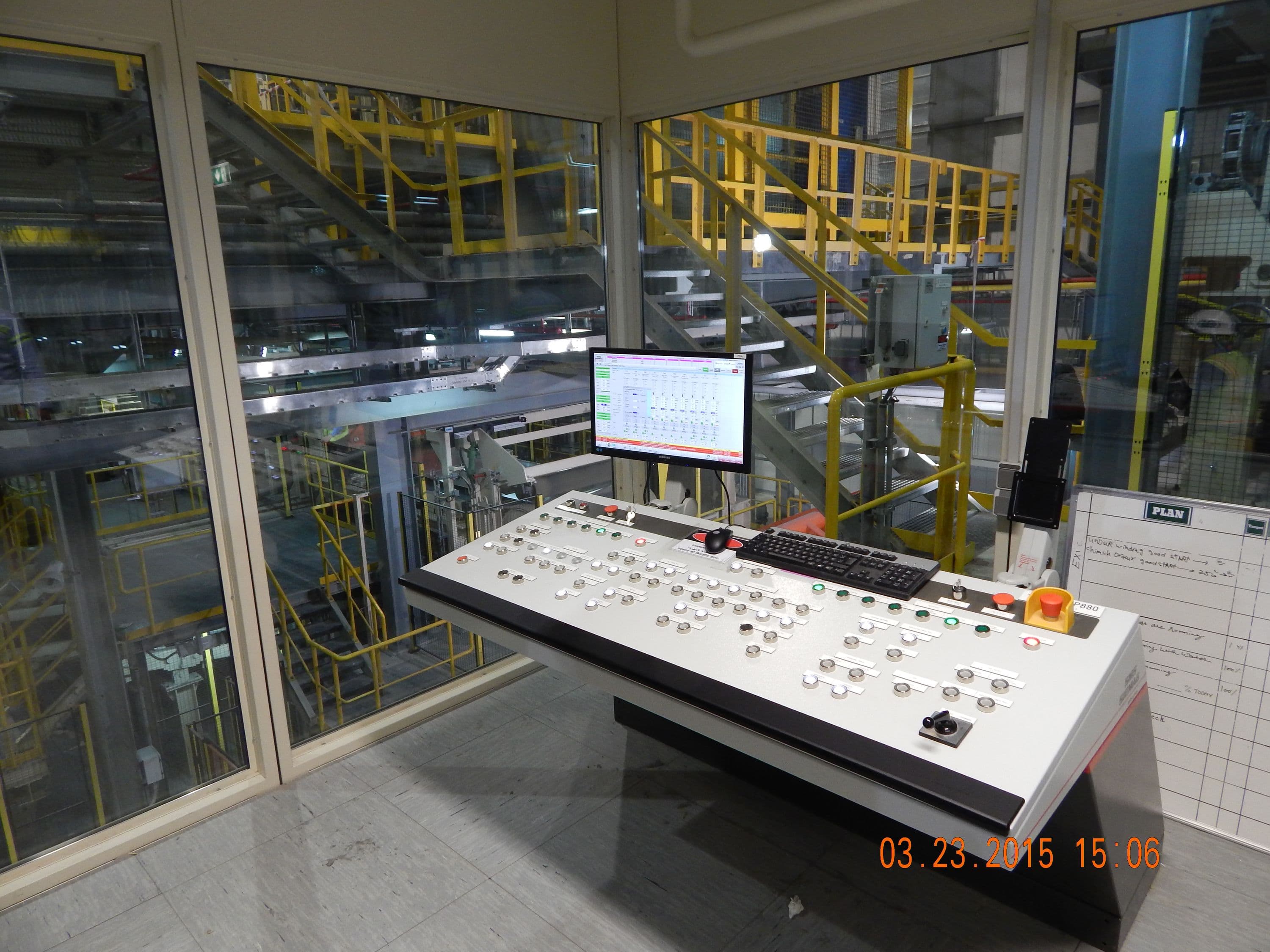
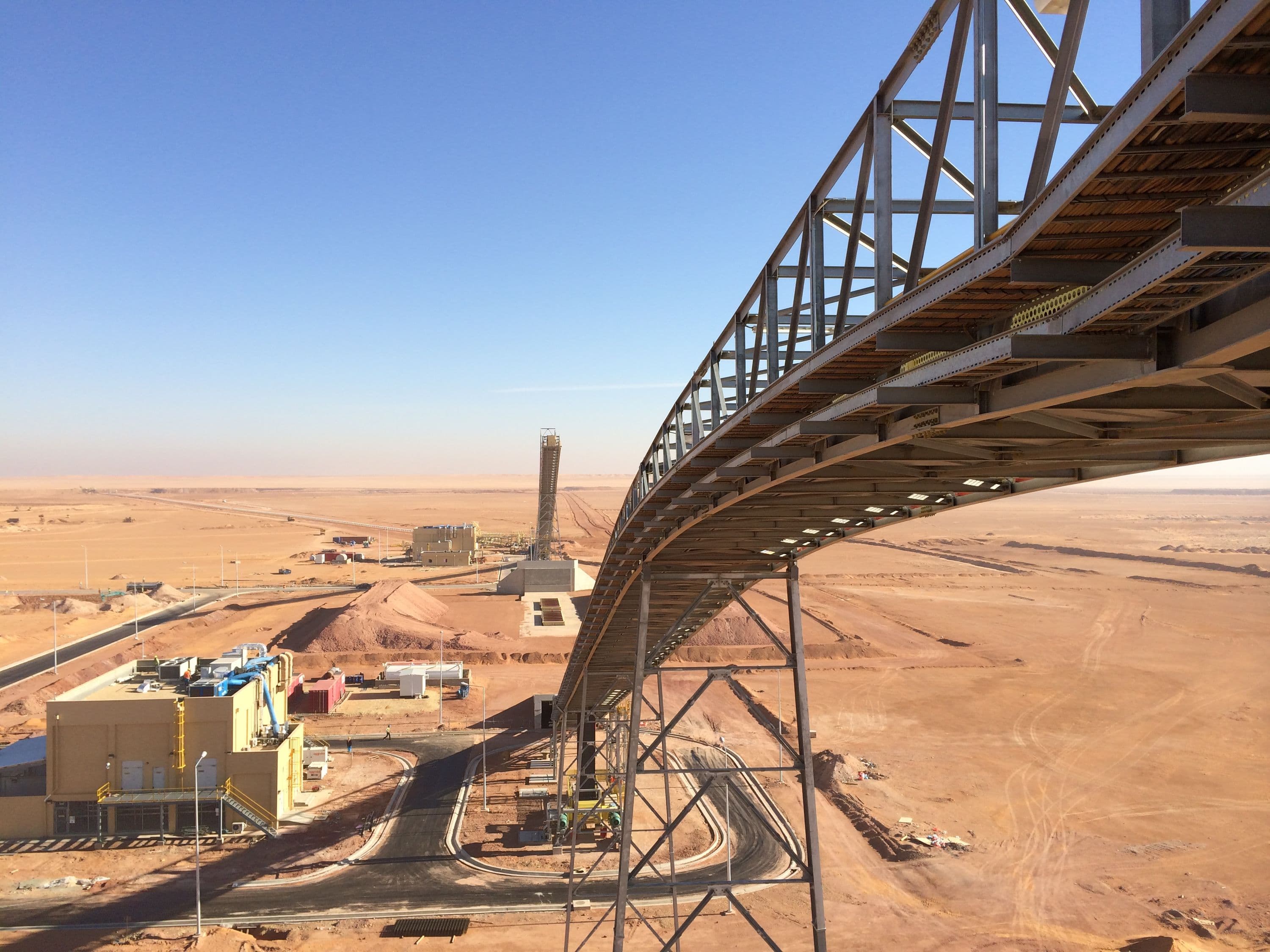
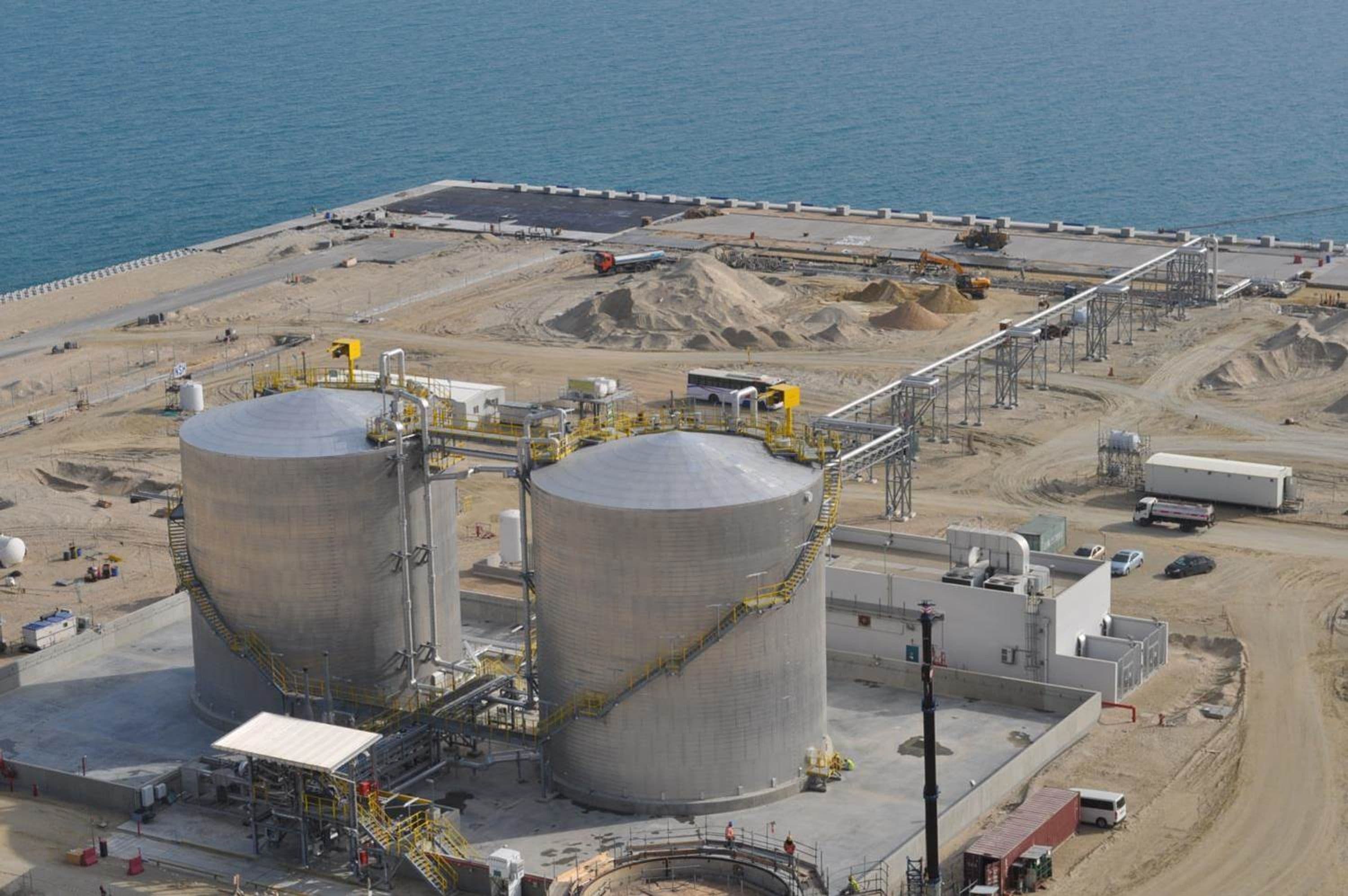
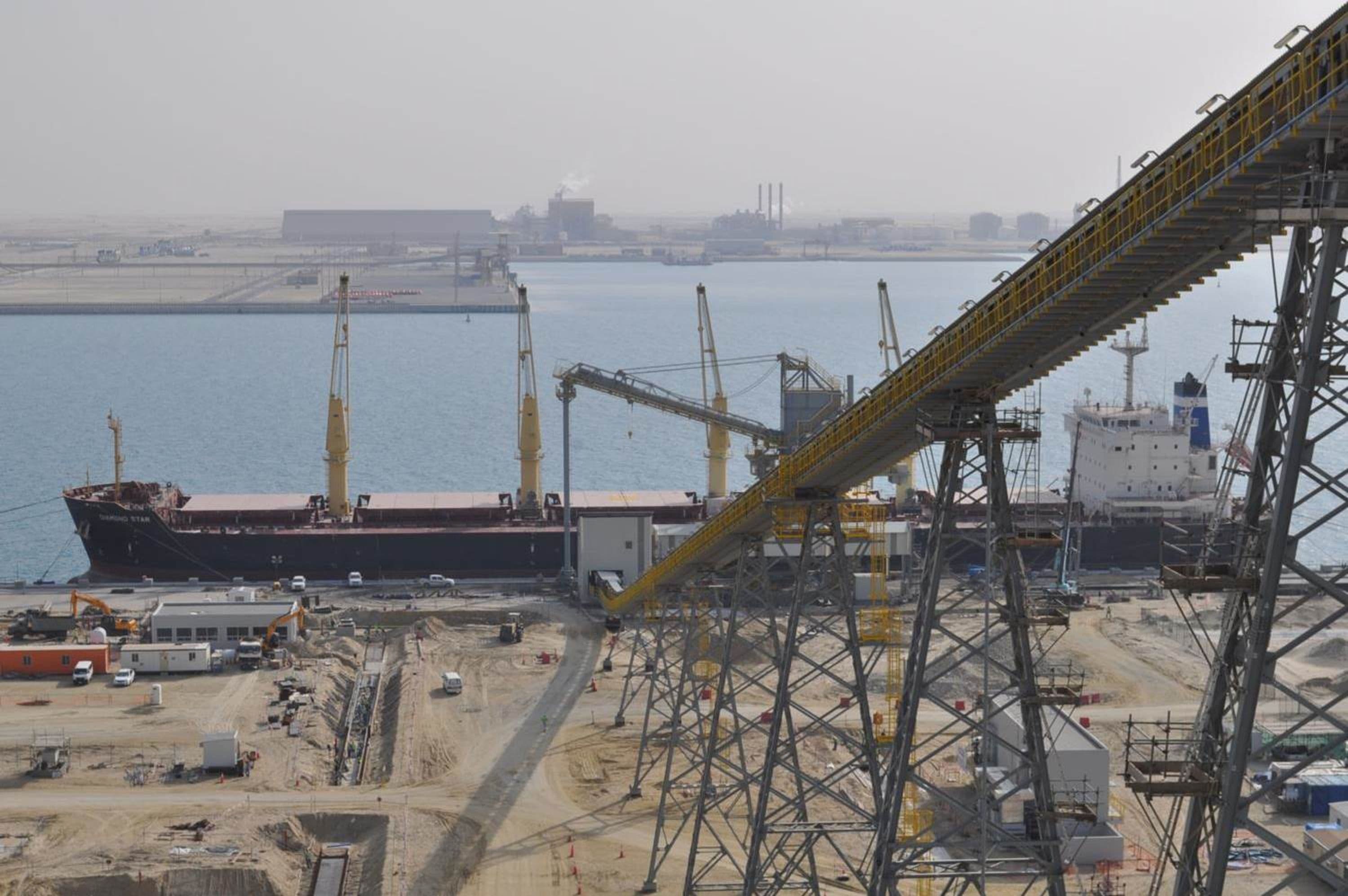
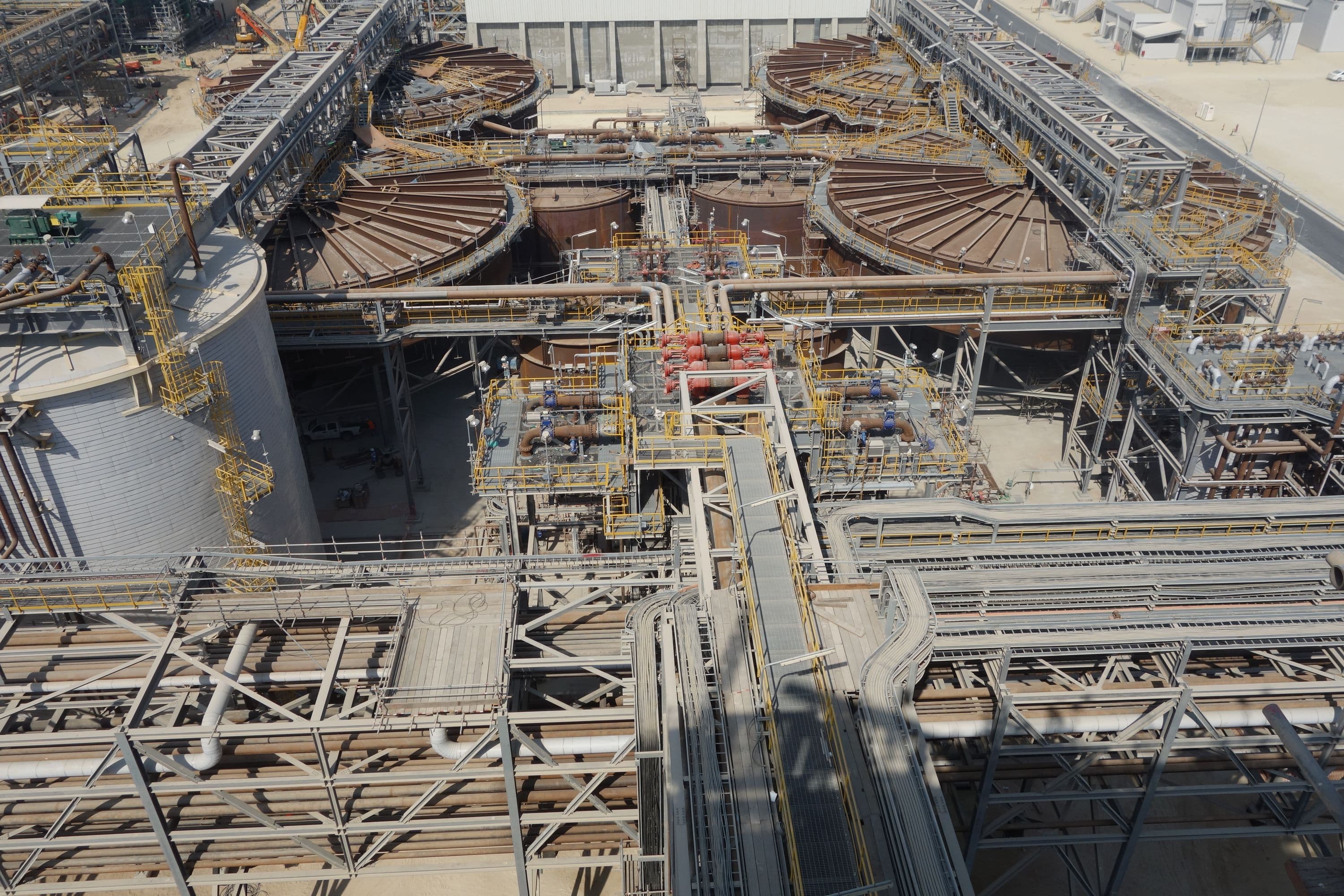
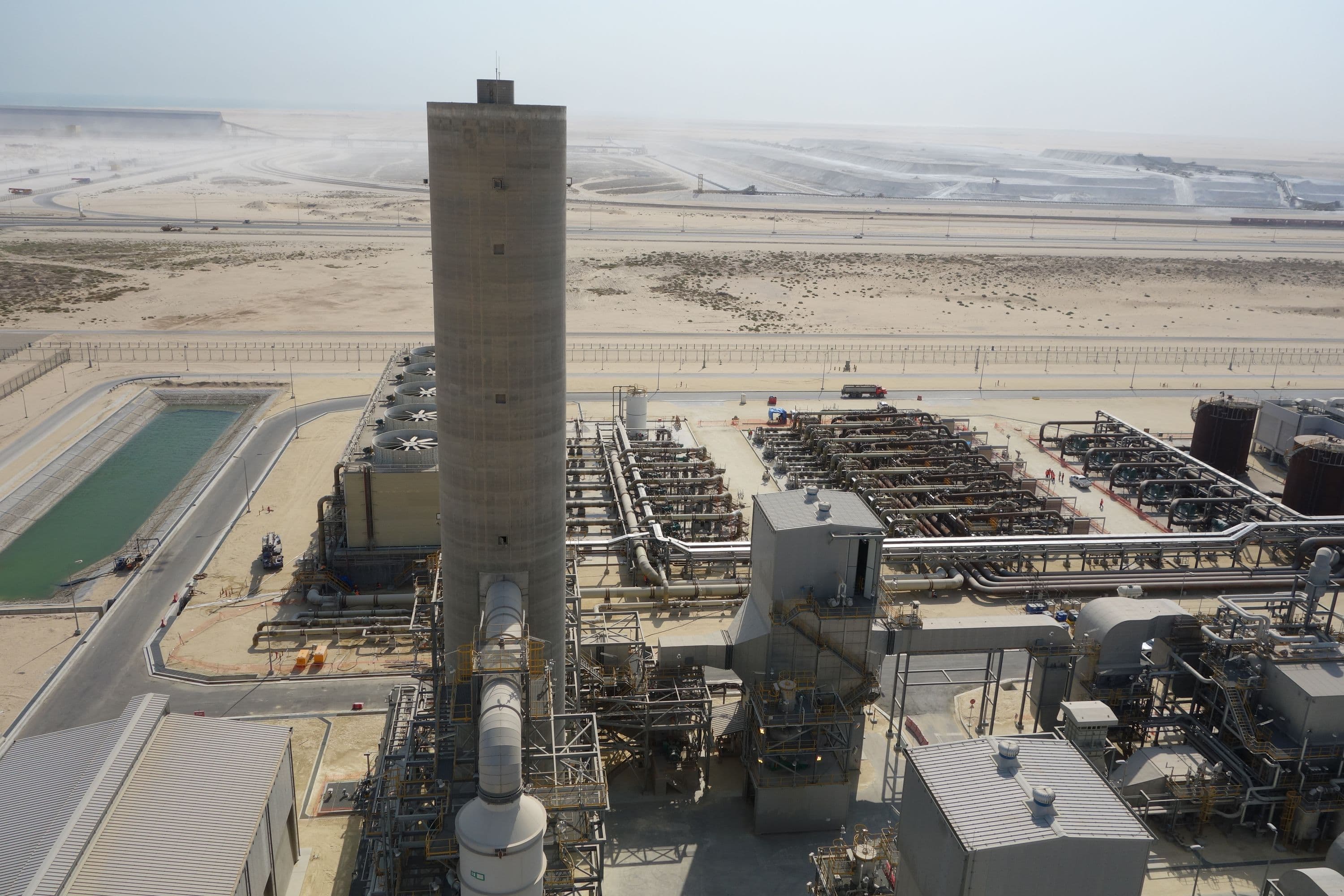
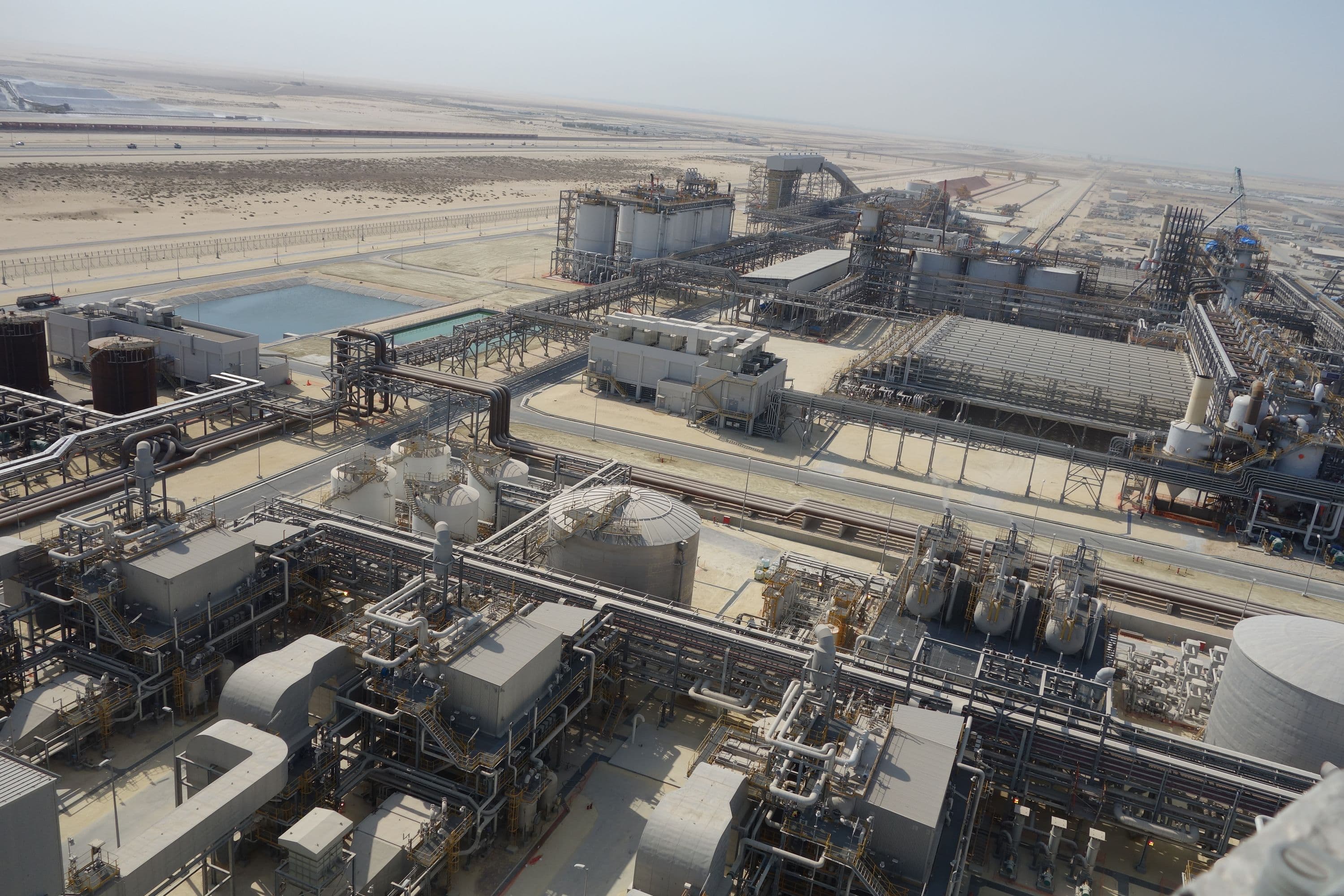
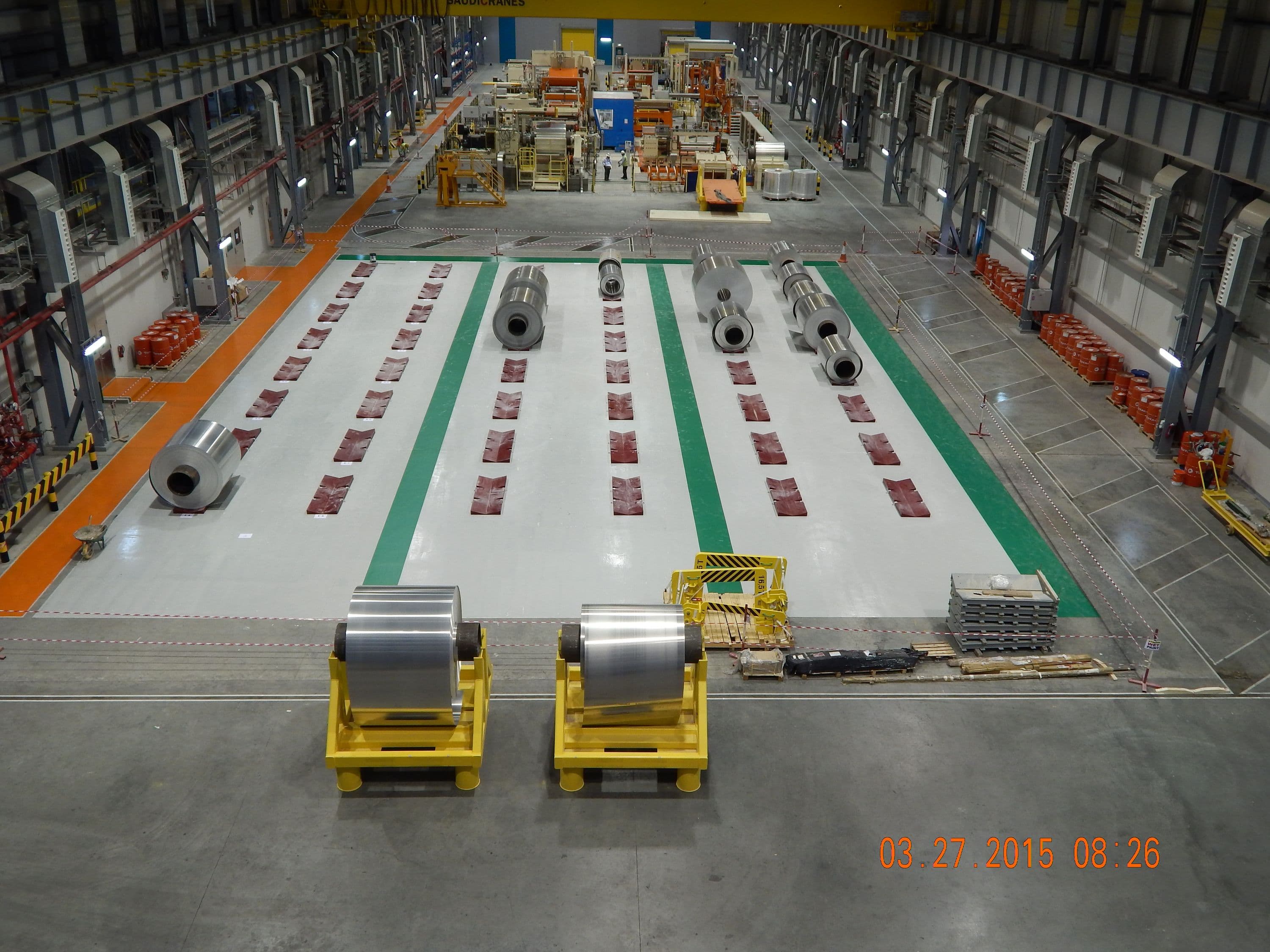
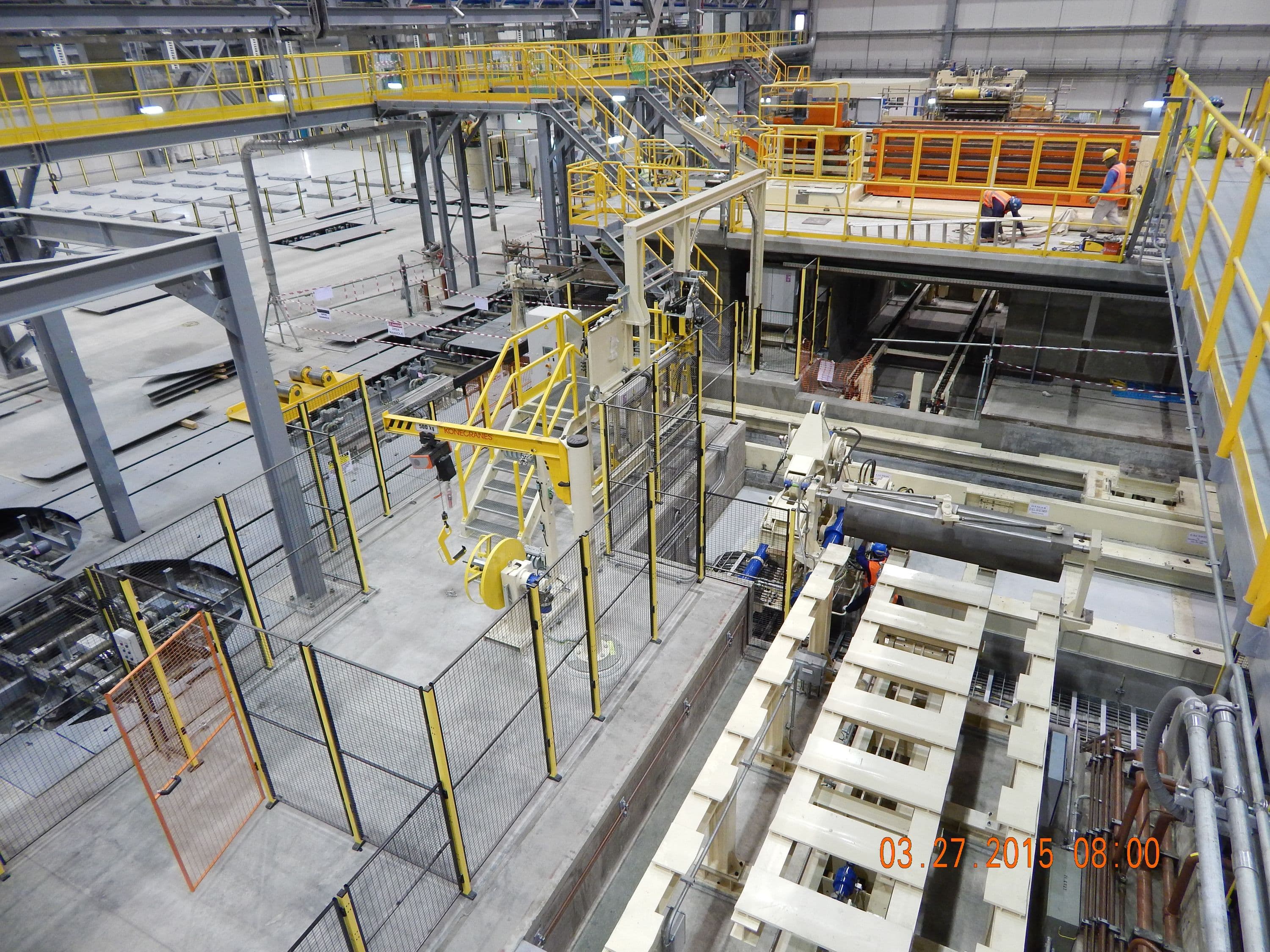