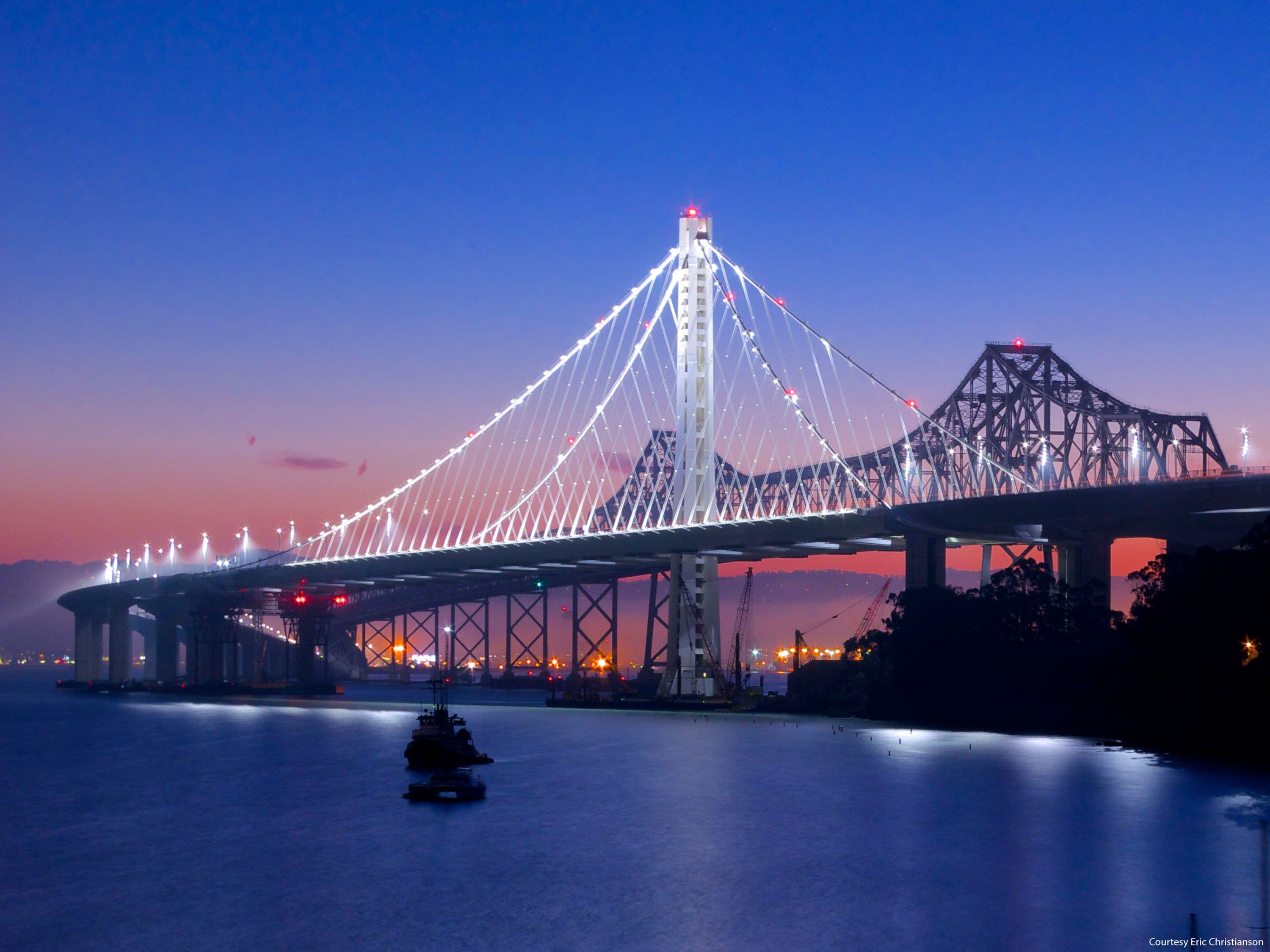
Caltrans San Francisco-Oakland Bay Bridge Construction
Client: California Department of Transportation (Caltrans)
Location: San Francisco, CA, U.S.
Business Segment: Urban Solutions
Industry: Infrastructure

Executive Summary
The American Bridge/Fluor Joint Venture (ABFJV) constructed the $1.8-billion, 625-meter-long East Span of the San Francisco-Oakland Bay Bridge. This first-ever, single-tower, self-anchored suspension (SAS) bridge was the largest public infrastructure project in California's history. The bridge opened to traffic on the eve of September 2, 2013.
The project team met major construction milestones, including erecting the world's largest cable saddle on top of the steel tower at 495 feet (151 meters) and installing the final, main cable strand on the SAS bridge five weeks ahead of schedule.
The ABFJV team designed a cable hauling system to install the strands from the deck anchorage on the eastside, over the tower saddle, around the west cap beam, back through the tower saddle and finally into the cable anchorage on the eastside.
The cable erection equipment includes a primary strand hauling system, or tramway, and secondary hauling systems with transfer arms to float and install the strands into the deviation saddles on the west side and through the tower saddle. The installed 137 strands were then compacted into a bundle and wrapped with zinc paste and stainless steel S-wire before being painted.
Banner photo courtesy of Eric Christianson.
Client's Challenge
The eastern span of the Bay Bridge was damaged during the 1989 Loma Prieta earthquake when a section of the bridge's upper deck collapsed onto the lower deck. While the damage to the bridge was relatively minor, its structural failure underscored the seismic vulnerability of this major transportation link for the San Francisco area. The California Department of Transportation (Caltrans) specified that the bridge be able to withstand major seismic activity. Additionally, in an area known for its signature bridges, the aesthetics of the bridge also demanded construction excellence.
The suspension cable system was a major construction challenge, with a single cable anchored on one end of the bridge crossing over the top of the single tower, looping under the span's opposite end and crossing back over the tower top to the other side. Additional challenges included construction of the falsework supporting the new road deck and the single tower, followed by the transfer of the road decks to the suspension cable system and incorporation of elements that provide seismic stability.
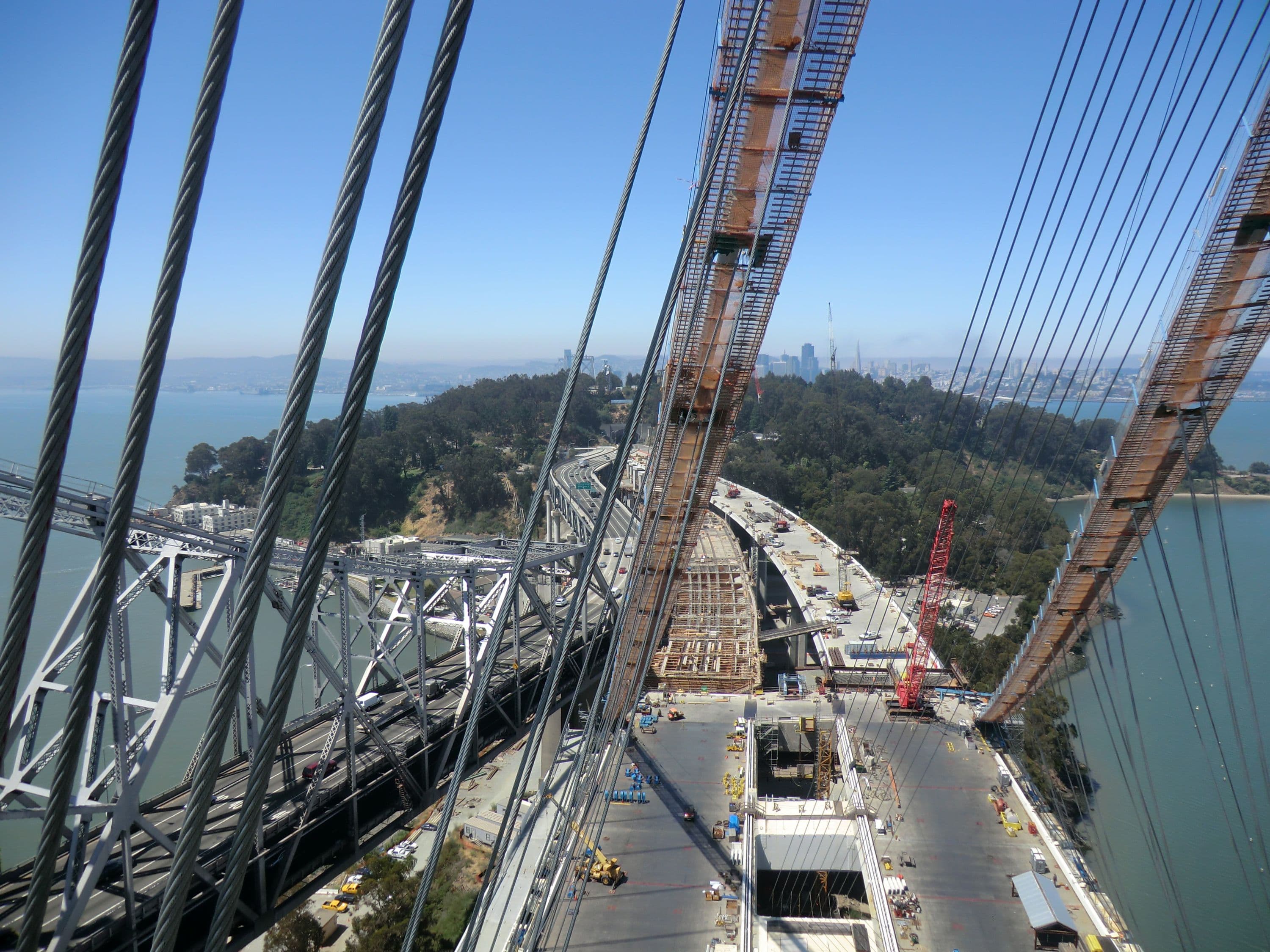
Fluor's Solution
The American Bridge/Fluor joint venture (ABFJV) began construction on the SAS portion of the bridge in 2006. The bridge officially opened to traffic on the eve of September 2, 2013.
The SAS, together with the Skyway and Oakland Touchdown, completed the east span of the Bay Bridge. Initial construction activities included logistics planning and long-range procurement. A 400-foot long, 1,700-metric-ton capacity shear leg crane barge was constructed to lift the massive segments of the deck and tower. Bridge components were fabricated in the United States, Europe and Asia. A secondary office was established in Shanghai, People's Republic of China, to oversee production of the main structural steel fabrication and supply.
ABFJV erected a falsework structure to support the new road deck. Bridge components shipped via eight shipments, arriving every two months from China. Road deck segments were lifted from the barges onto the falsework by the shear leg crane barge, with the road deck in-place after 28 lifts. The 160-meter tall single tower from which the bridge is suspended was completed concurrently. After installing the 800-mm diameter main cable and suspender cables, the deck weight was transferred from the temporary falsework to the main cable.

Conclusion
The completion of the SAS Bridge provided the San Francisco Bay area with not only a breathtaking bridge but also a sound structure that will withstand major seismic events and serve as an emergency lifeline route for disaster responses. ABFJV provided new levels of innovation and an exacting precision in work performance and construction quality to deliver a signature bridge that meets these requirements.
This project exemplified the high-level coordination required among contractors, agencies and the public to make sure all elements of this highly complex, multi-segmented, mega project came together as planned.
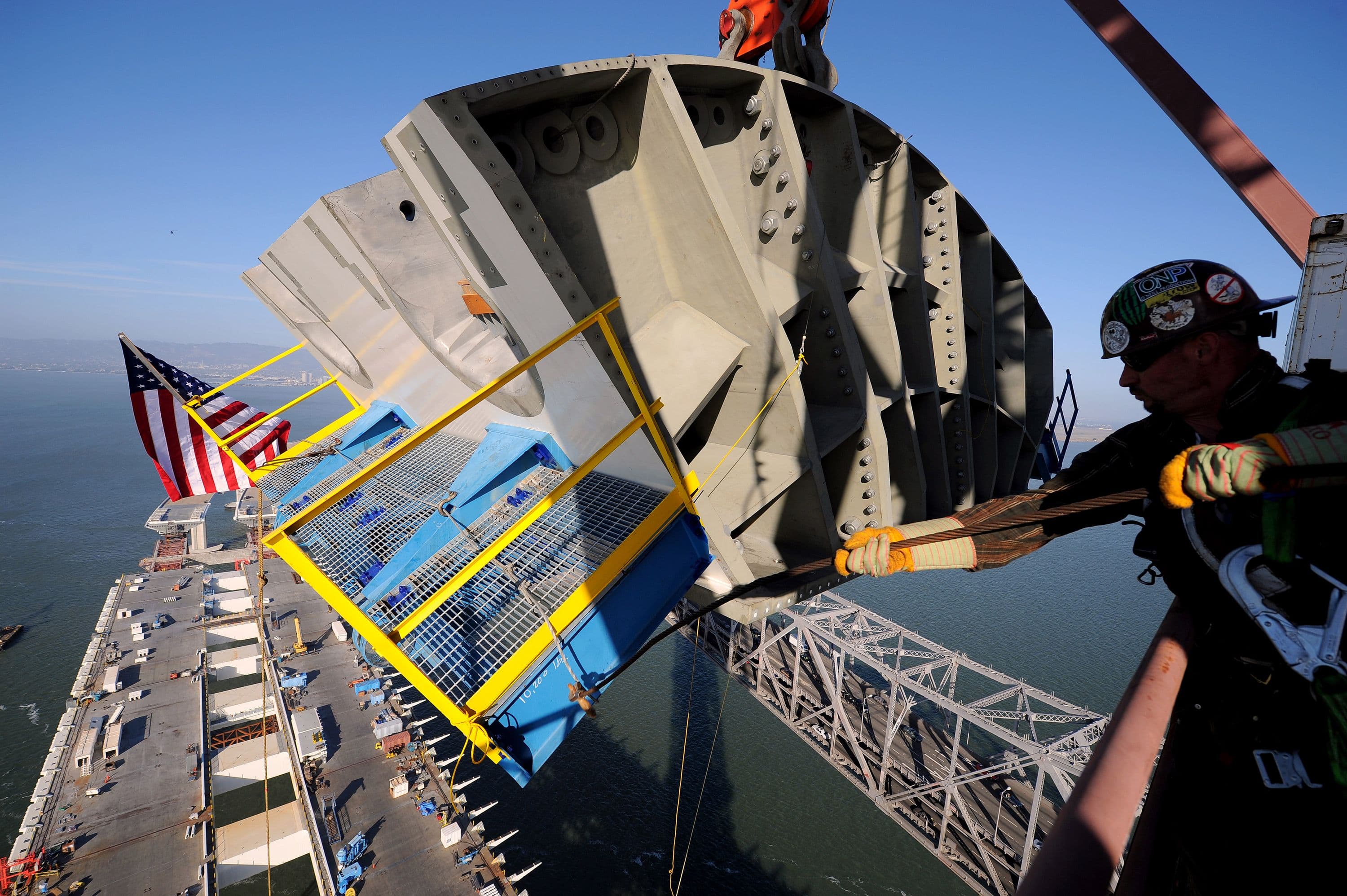
Project Gallery
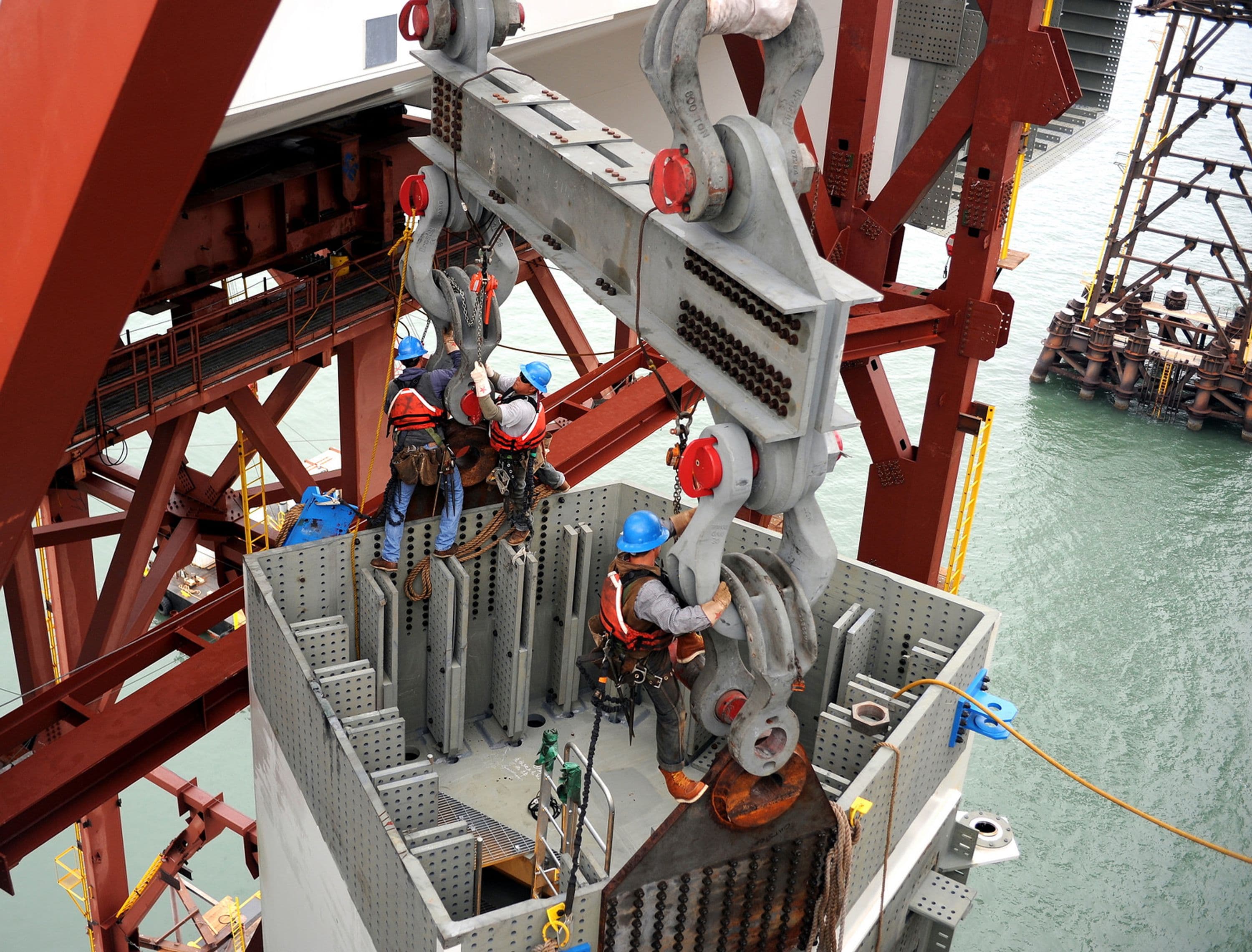
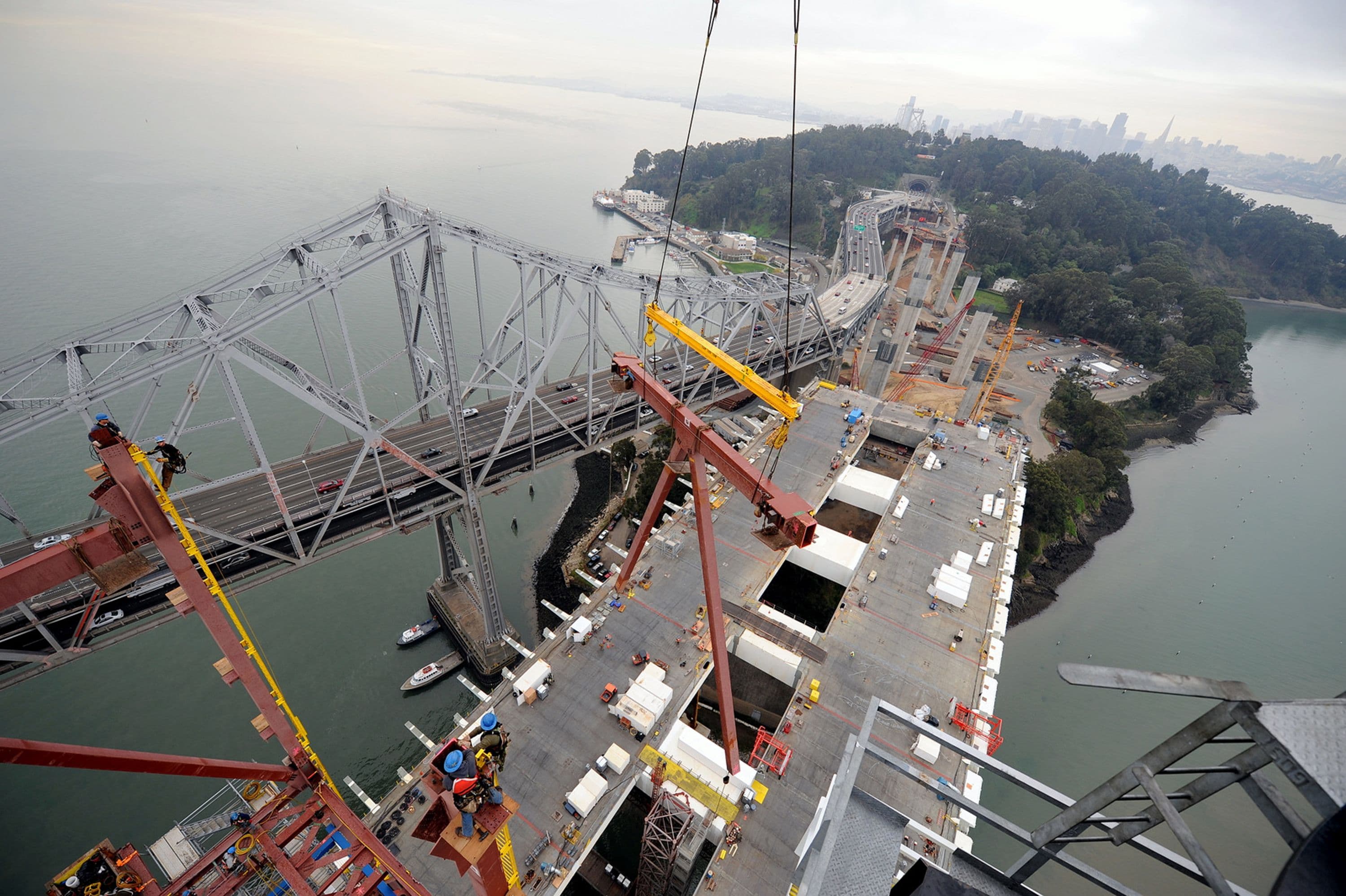
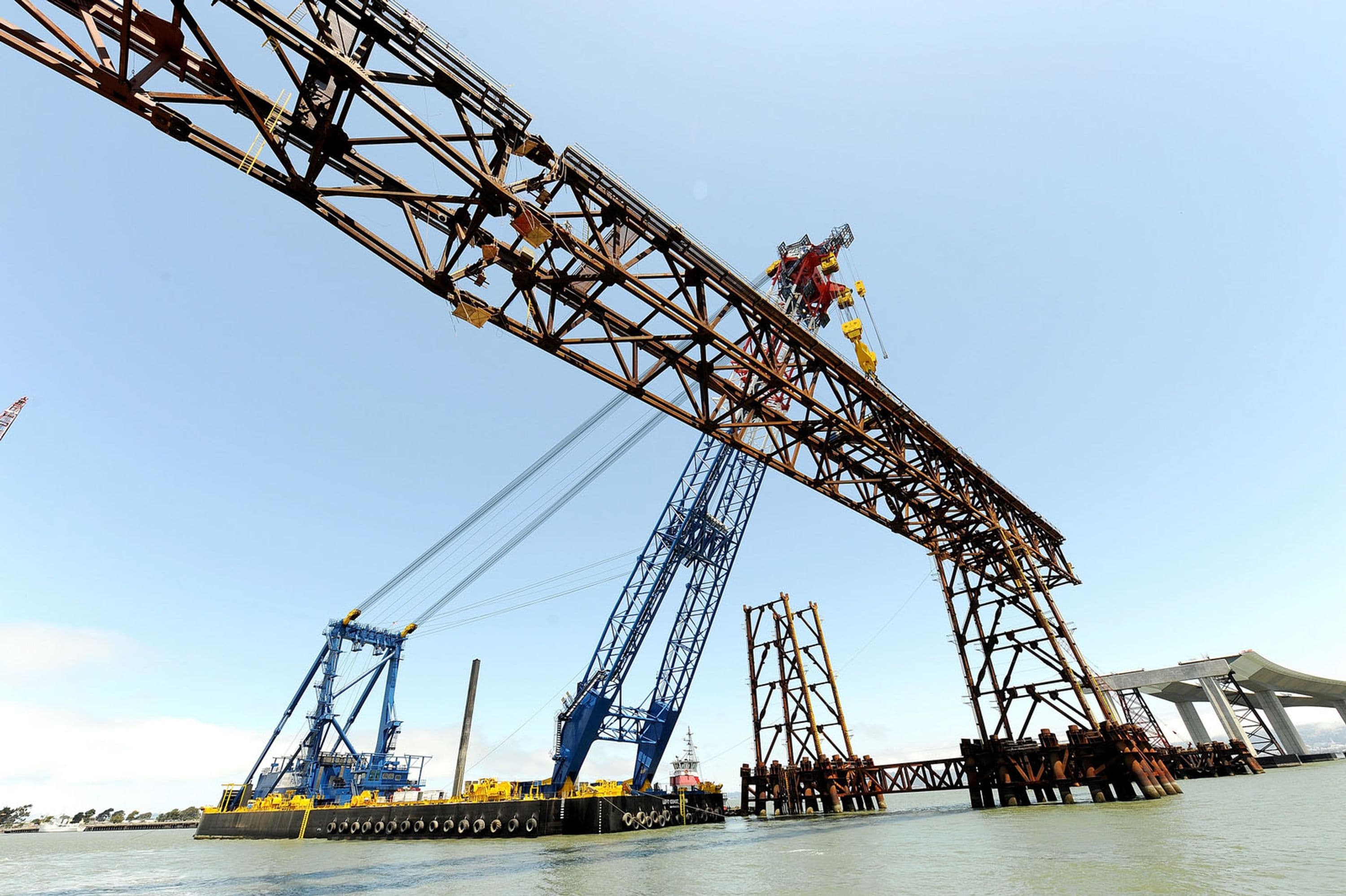
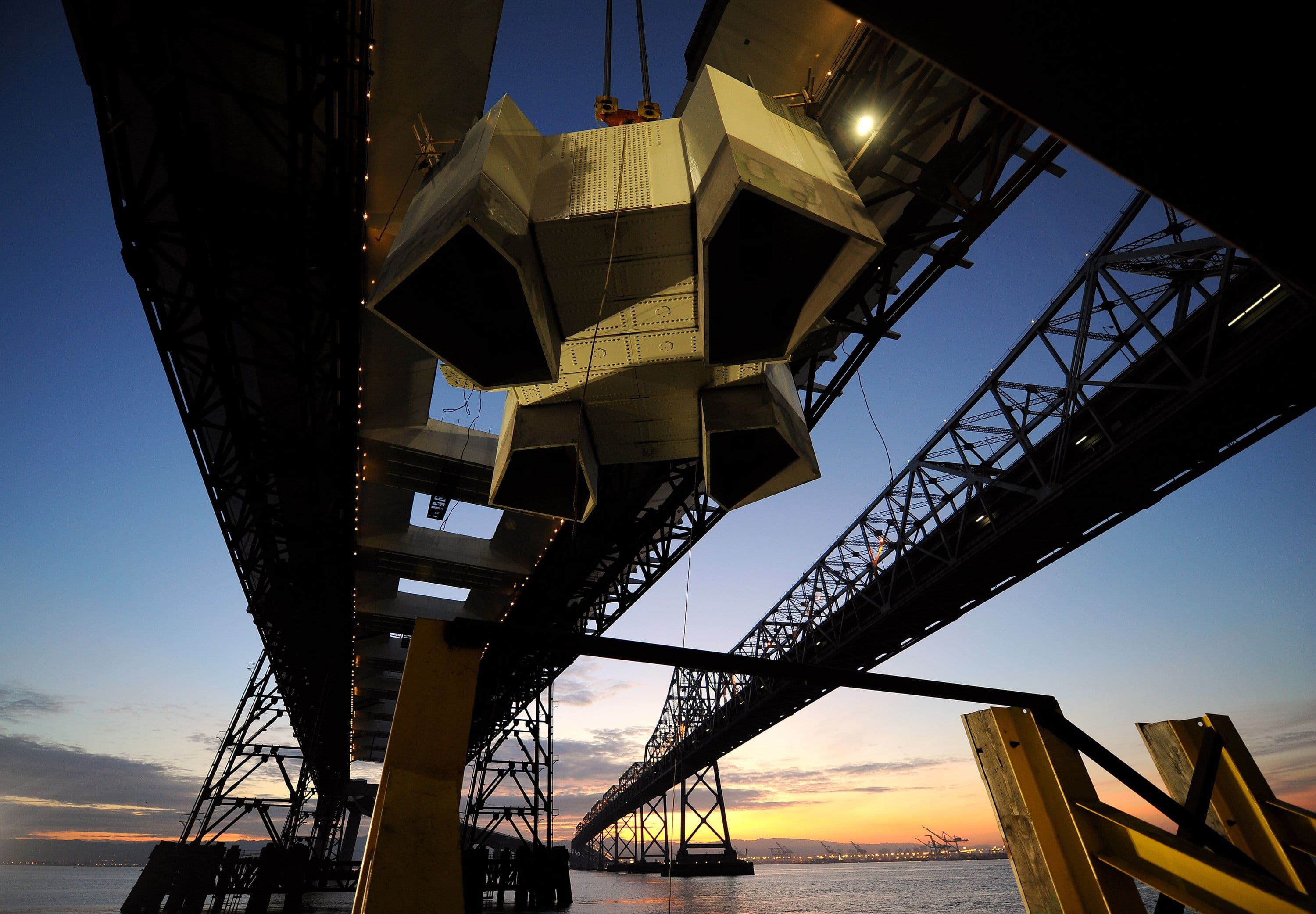
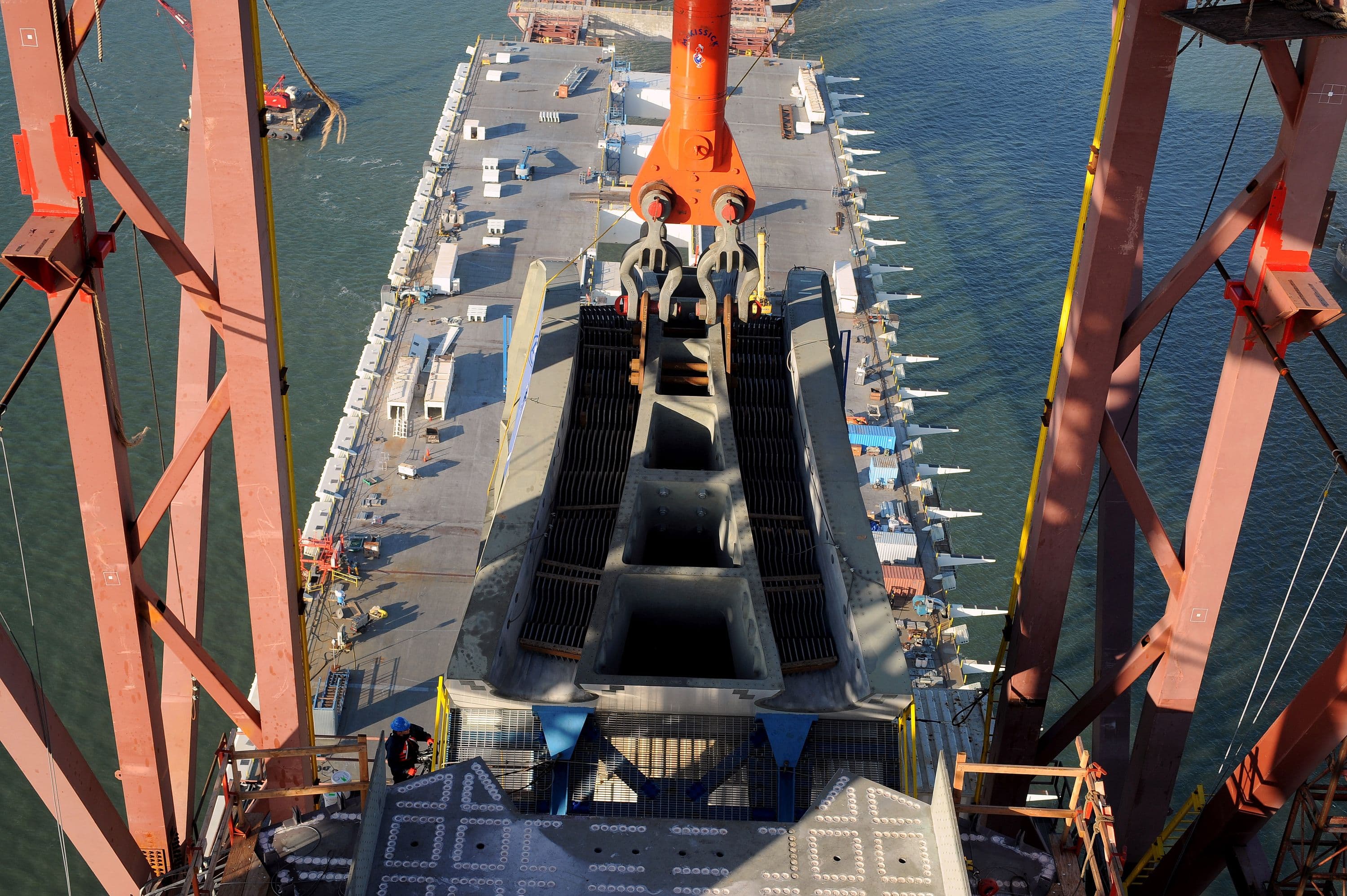
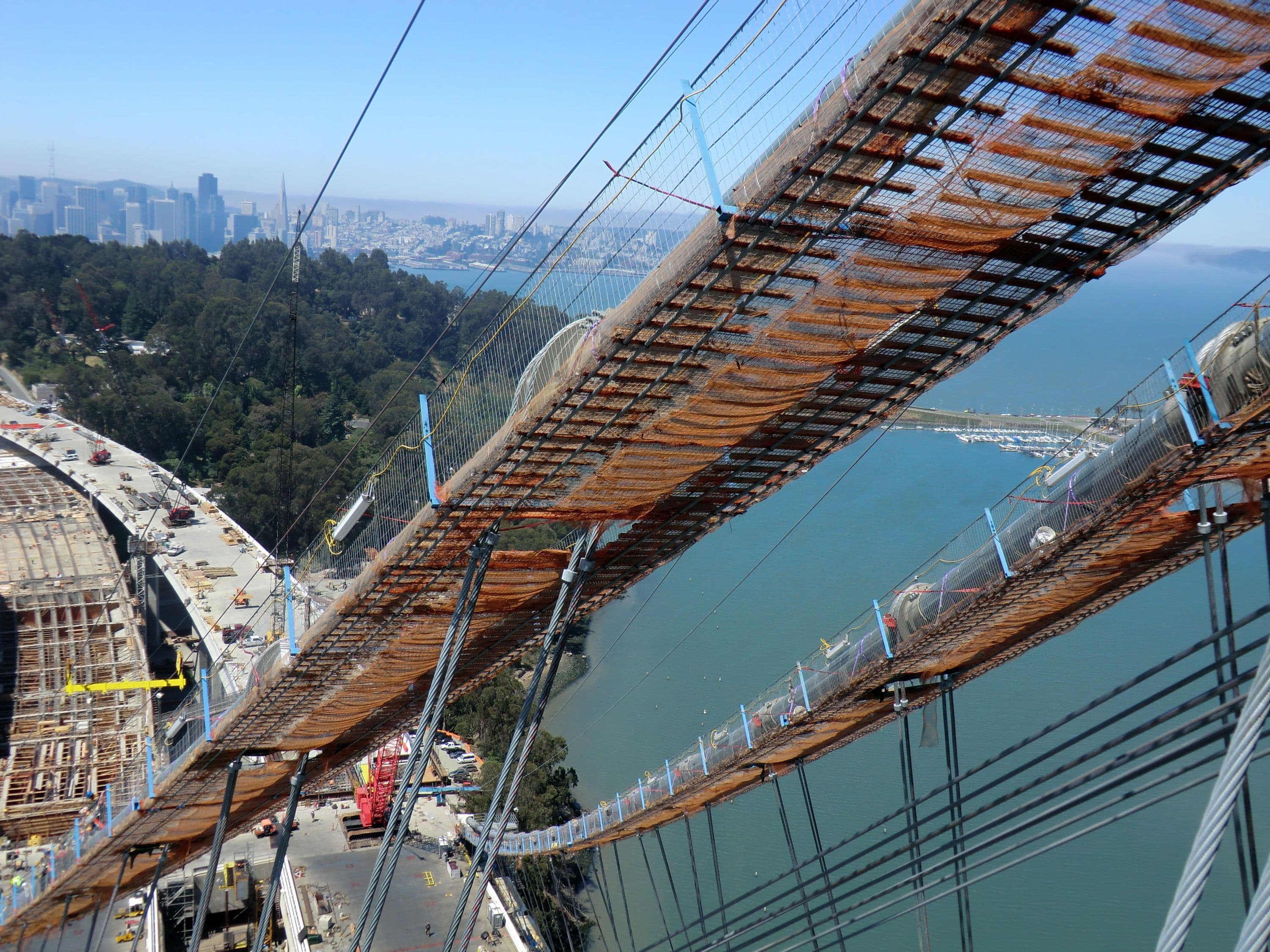
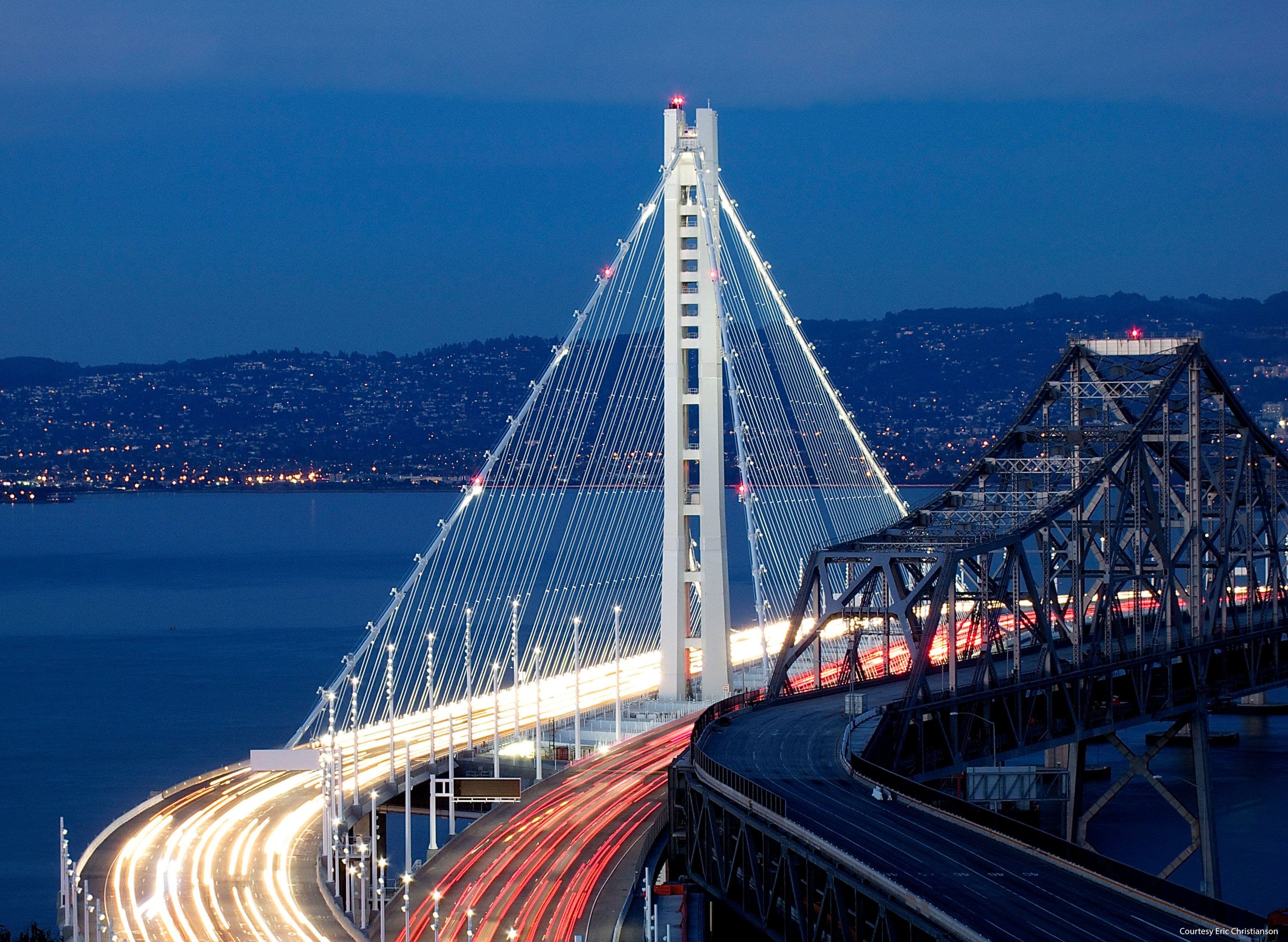