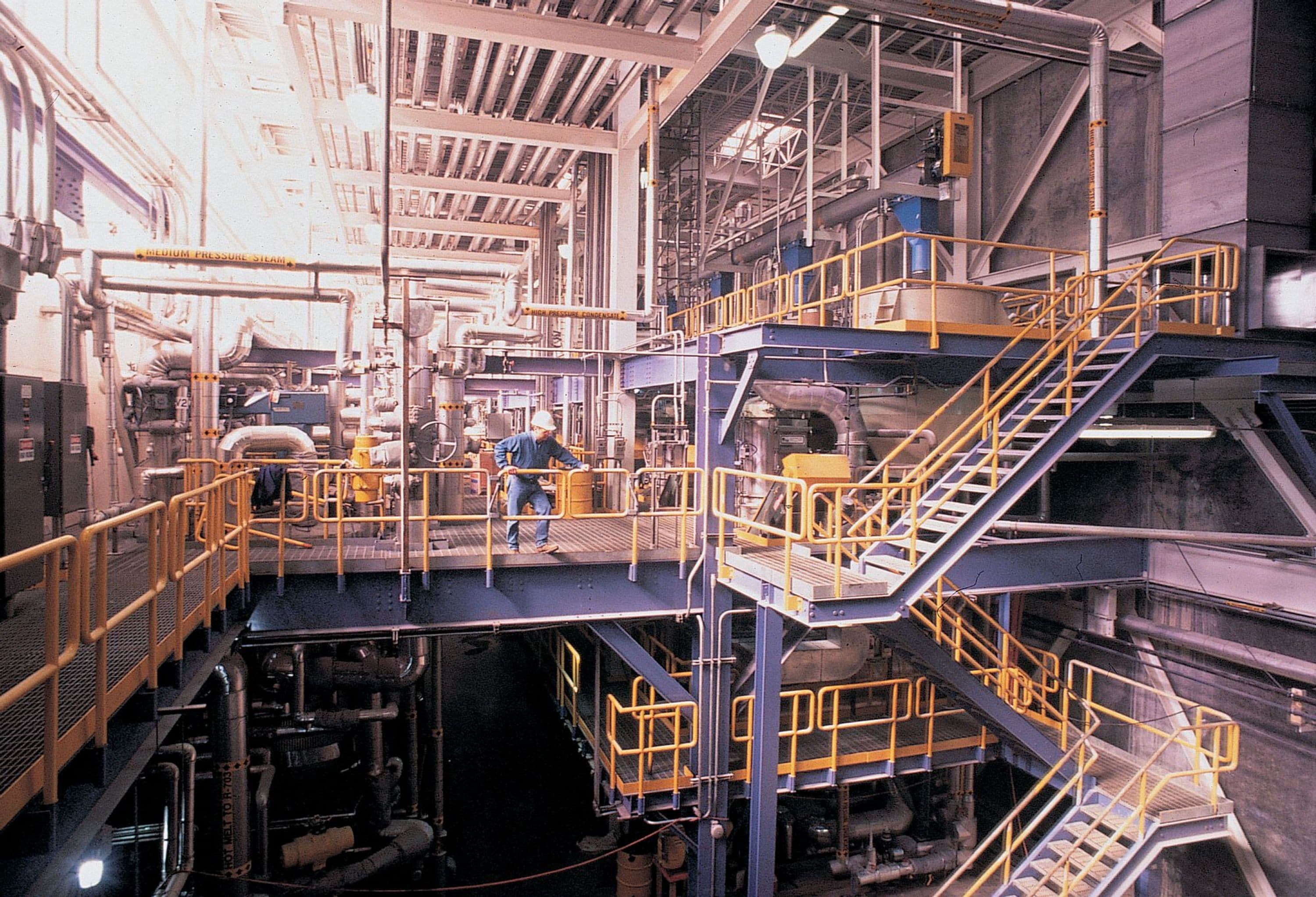
Milliken Carpet Dyeing Facility Rebuild-181 Days - Engineering & Construction
Client: Milliken
Location: LaGrange, GA, U.S.
Business Segment: Urban Solutions
Industry: Manufacturing
Services: Maintenance

Executive Summary
After a devastating fire destroyed Milliken's Live Oak dyeing and carpet finishing plant on January 31, 1995, Roger Milliken called on Fluor to assess the damage and plan for a rebuild with an aggressive six-month schedule, using upgraded technology, to meet the company's fall schedule.
Within hours, we had mobilized a rapid response team to assess the damage and set up operations near the destroyed plant. We brought people from five U.S. cities and three countries to form a workforce that would work around the clock to meet the aggressive schedule.
Six months later, Milliken's Live Oak plant opened for business.
The Milliken Fire Rebuild project received Fluor's Hugh Coble Project Excellence Award in 1995. The award is based on outstanding performance in several areas, including safety, value creation and client and community relations.
Client's Challenge
The center of Milliken's operation was the Live Oak facility, where broadloom and tile carpet were finished in areas such as carpet tile backing, carpet tile printing, broadloom carpet backing, broadloom carpet printing, compounding, dye and chemicals mixing.
Roger Milliken declared that the rebuild would be a state-of-the-art finishing plant and required that the plant be ready for business in six months, a third of the 24 months usually needed to build such a plant.
Fall is the busiest season for the carpet business, but Milliken executives knew this was a chance to build a world-class textile plant with the most modern machines, systems and technology.
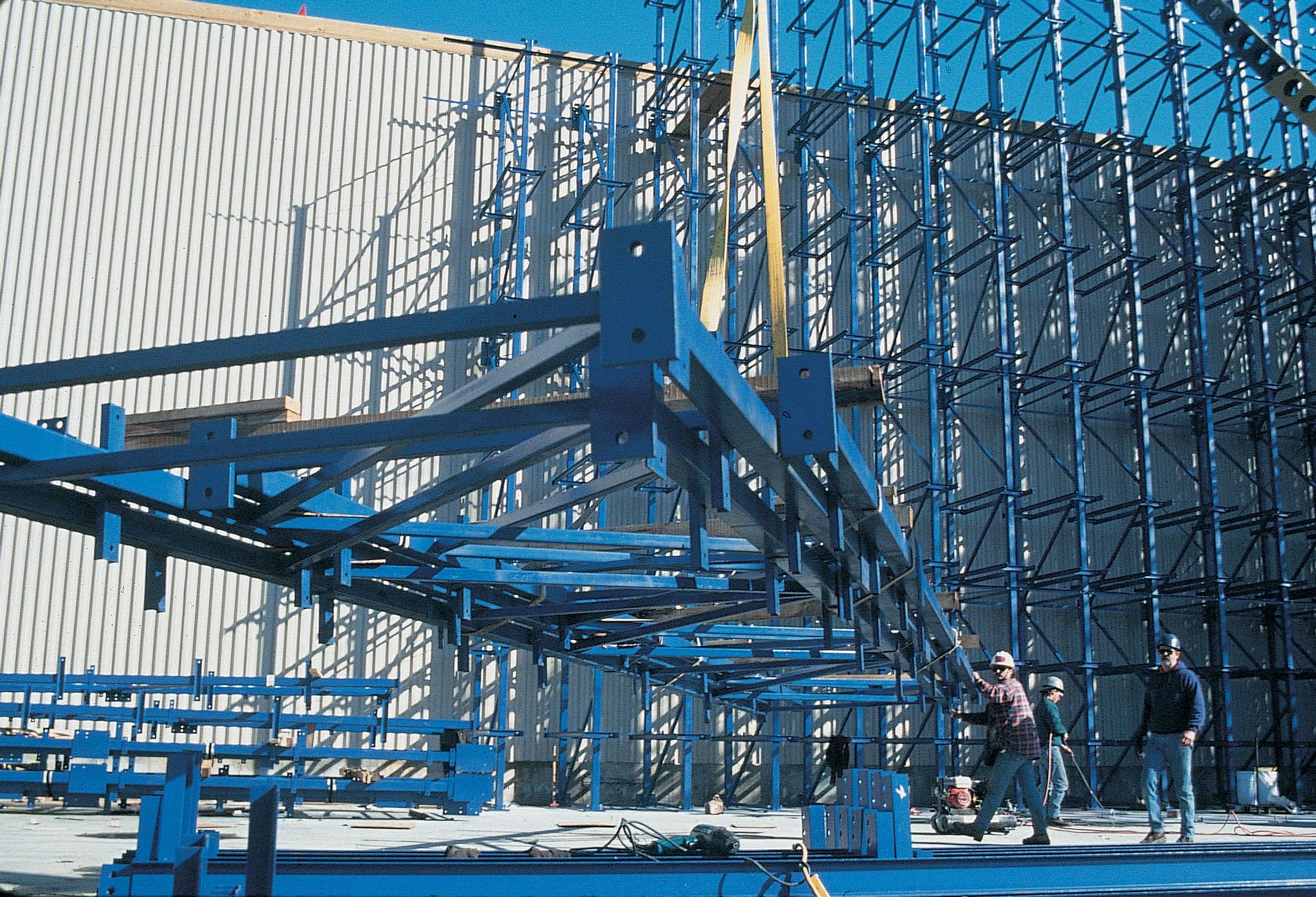
Fluor's Solution
Within hours, our team was onsite, surveying damage and planning the rebuild. We began mobilizing engineers, craft workers, contractors, suppliers and managers from offices around the world. The 250 engineers worked in "plywood city," a building in which offices were divided by sheets of plywood, along with engineering teams from Milliken and other project participants.
We organized the engineering project into eight area teams, each taking ownership and responsibility that included its own purchasing and scheduling. It was the only way to get the job done, as far as Fluor was concerned, because the engineers were there to react quickly to changes.
Work took place 12 hours a day during two shifts, at night lit by football stadium lights. The need for electricians, welders, engineers and construction managers skyrocketed, peaking at 3,300 in early June, 2,500 of whom were hired from the pool of professionals in Fluor. Before anyone could start work on the project, he or she had to go through Fluor's safety training program. Safety would not be compromised.
To support the fast track project, we were able to call on our global network of suppliers to provide critical shipments of steel and other materials for construction. A Fluor subsidiary provided construction equipment, tools and materials.
In completing the Milliken project, we met challenges while also having rare opportunities. For example, engineers were integrated with construction personnel on the area teams. Everyone learned from the experience.
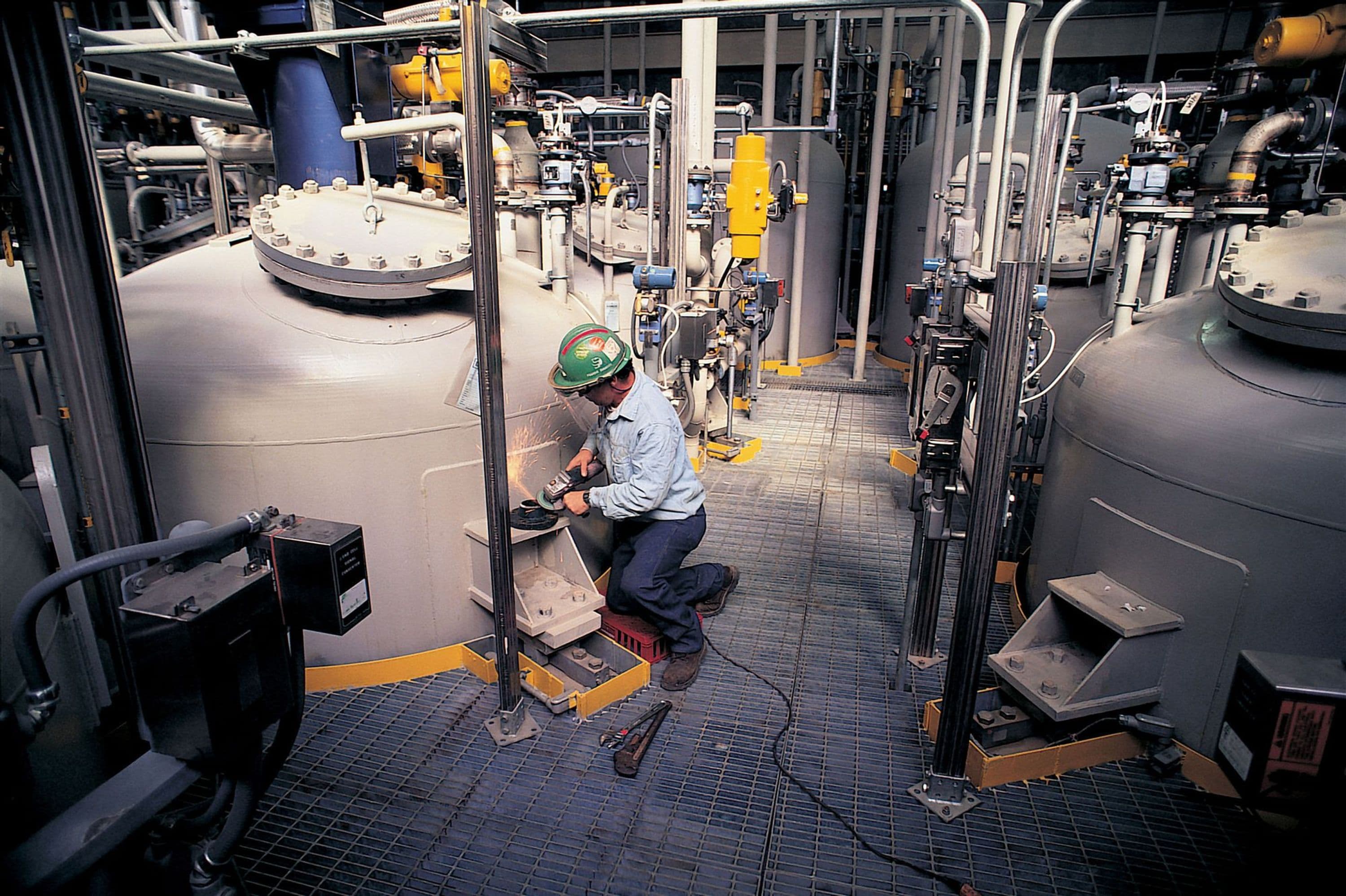
Conclusion
Fluor showed our capability to work at a fast pace and under challenging conditions so that the first plant product came off the line 15 minutes before the deadline. The project manager said the work had been “a 27-month project compressed into six months . . . like a continuous cavalry charge.”*
Mr. Milliken stated, “The carpet industry is competitive, and we do not want to lose our share of the market. We knew Fluor could help us make our target date.”**
* The Atlanta Journal, August 2, 1995; also in Horizons article
** Fluor Horizons August 1, 1995
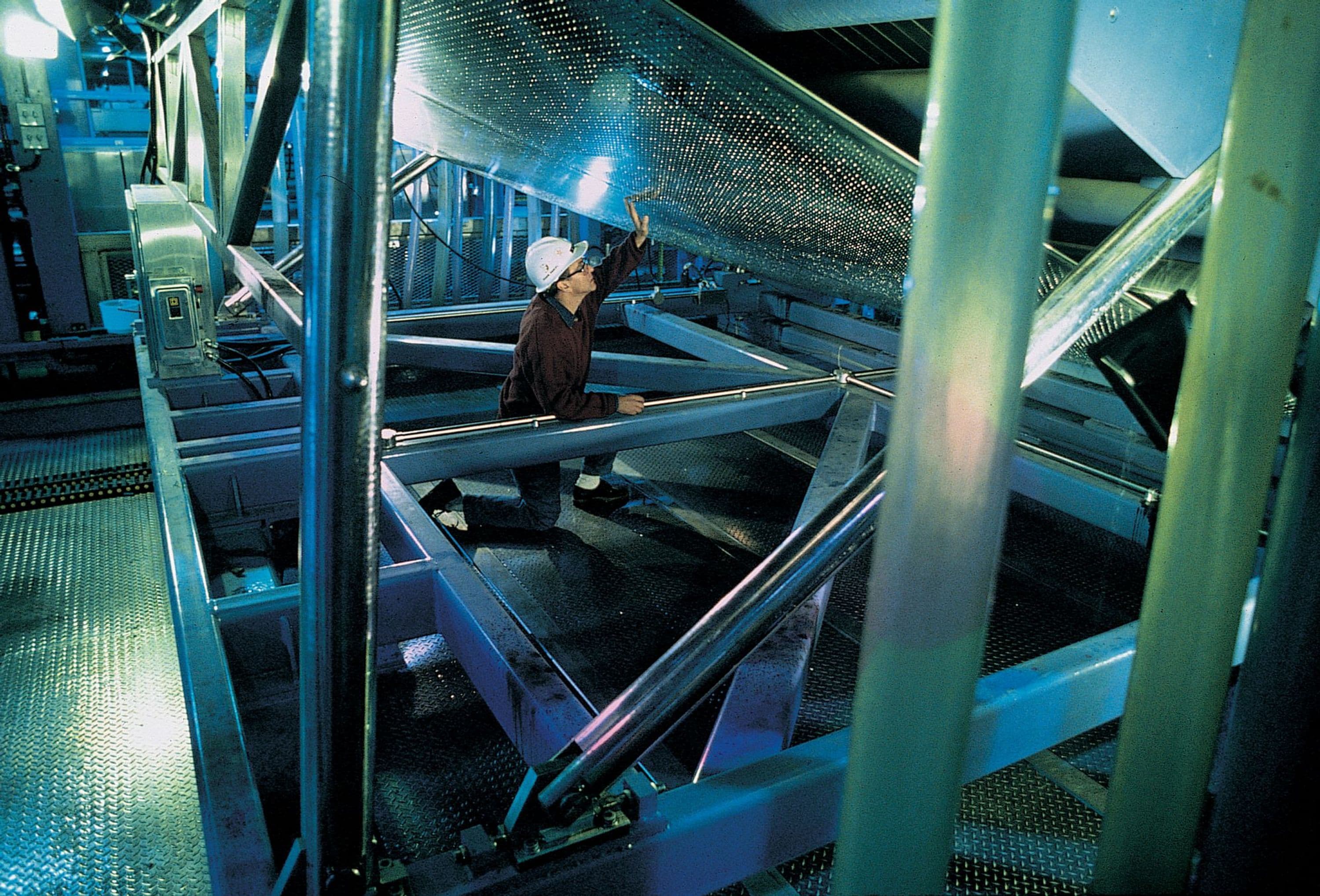